Exploring the Benefits of Aluminum Injection Molding in Today's Manufacturing Industry
By:Admin
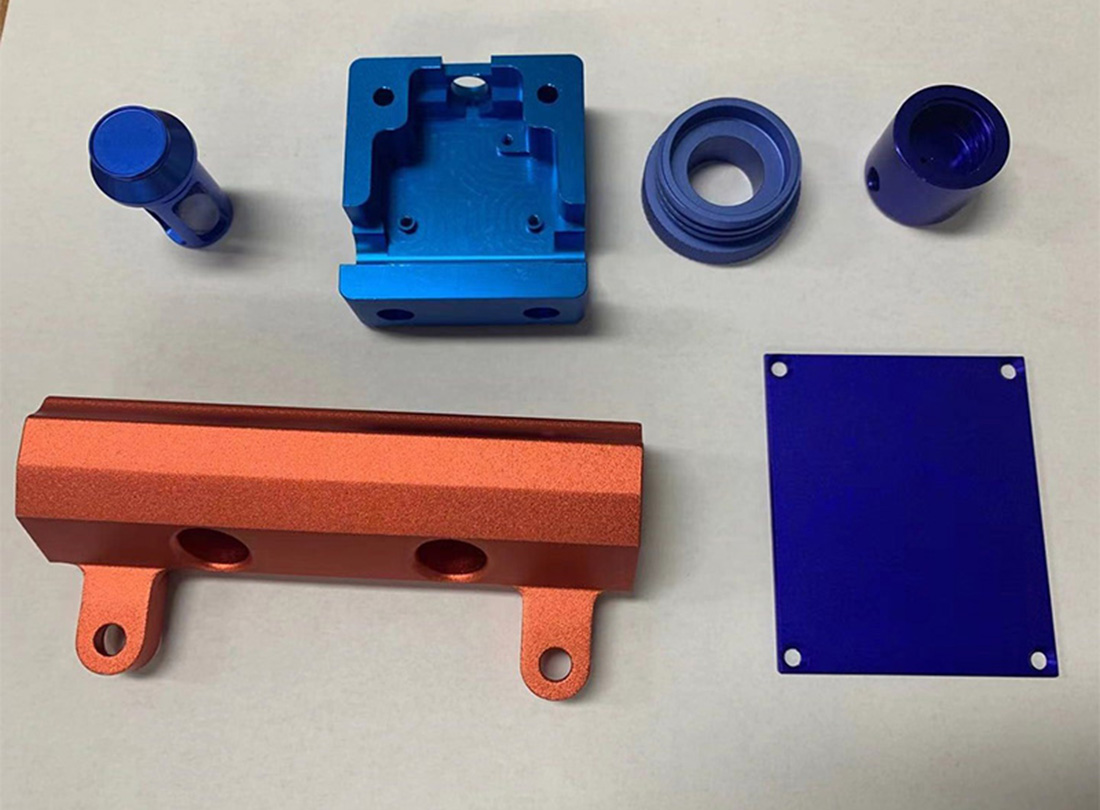
Title: Revolutionizing Manufacturing: Aluminum Injection Molding Sets New Industry Standards
Introduction:
Innovation continues to be the driving force behind advancements in the manufacturing industry. Among the latest breakthroughs is the revolutionary technique of aluminum injection molding. This cutting-edge manufacturing process has the potential to reshape various sectors by providing unique advantages such as cost-effectiveness, increased design flexibility, and enhanced production efficiency. In this article, we delve into the details of aluminum injection molding, exploring its benefits, applications, and the promising future it holds.
Understanding Aluminum Injection Molding:
Aluminum injection molding is an advanced manufacturing technique that combines the versatility of plastic injection molding with lightweight and durable aluminum materials. This process involves injecting molten aluminum under high pressure into complex and intricate molds, allowing for the creation of intricate parts and components with exceptional precision. The process takes advantage of the desirable properties of aluminum, including its high strength-to-weight ratio, corrosion resistance, and excellent thermal conductivity.
The Company's Role:
The trailblazers in aluminum injection molding technology, [Company Name], have been at the forefront of the industry, leading in research, development, and implementation of this groundbreaking method. Their extensive experience and cutting-edge facilities have enabled them to refine and perfect the aluminum injection molding process, making it highly efficient and adaptable to various manufacturing requirements. The company's dedication to continuous innovation has positioned them as a driving force behind the widespread adoption of aluminum injection molding.
Applications and Industries Transformed:
The advent of aluminum injection molding has had a transformative impact across numerous industries, offering a wide range of applications and benefits. In the automotive sector, lightweight aluminum components produced through this process have revolutionized vehicle design, leading to improved fuel efficiency, better performance, and enhanced safety. Similarly, aerospace manufacturers are benefiting from the lightweight properties of aluminum injection-molded parts, resulting in reduced fuel consumption and increased payload capabilities.
Electronics and telecommunications industries can leverage the design flexibility of aluminum injection molding to create intricate and high-performance electronic enclosures and housings. The process also allows for the integration of additional features, such as heat sinks, resulting in improved thermal management and extended device lifespans.
The medical field is yet another sector where aluminum injection molding can make a profound impact. The ability to produce complex and sterile medical devices and implants made from lightweight yet durable aluminum materials opens new possibilities for enhanced patient care, improved surgical outcomes, and cost-effective medical solutions.
Benefits Driving Adoption:
The widespread adoption of aluminum injection molding can be attributed to the numerous benefits it offers. One of the most significant advantages is the cost-effectiveness of the process. By utilizing aluminum materials, which are relatively inexpensive, manufacturers can produce lightweight yet strong components without breaking the bank. This affordability extends to the tooling process as well, as aluminum molds are generally less costly than traditional injection molding molds.
Moreover, aluminum injection molding enables manufacturers to achieve intricate and precise designs that were previously unattainable. The ability to create complex geometries with exceptional accuracy allows for the integration of multiple functions into a single part, reducing assembly time and enhancing overall product performance.
Furthermore, the lightweight nature of aluminum components facilitates transportation and logistics, ultimately reducing costs and environmental impact. Aluminum's corrosion resistance properties also ensure long-lasting durability, making it an ideal choice for applications exposed to harsh environments or demanding conditions.
The Path Towards a Promising Future:
As aluminum injection molding continues to gain traction, researchers and manufacturers are working collaboratively to push its boundaries further. The ongoing advancement of this technology aims to enhance process efficiency, minimize cycle times, and explore possibilities for new alloy variants. Additionally, efforts are being made to streamline post-processing techniques such as surface treatments and finishing processes to ensure the highest quality standards.
Industry experts predict that aluminum injection molding will play a pivotal role in the wider adoption of electric vehicles, thanks to the efficiency gains and material advantages it offers. Furthermore, as sustainability and lightweighting remain key focus areas for many industries, aluminum injection molding will likely continue to grow, revolutionizing diverse sectors such as consumer electronics, renewable energy, and industrial manufacturing.
Conclusion:
Aluminum injection molding represents a transformative leap in the manufacturing industry. This innovative technique has revolutionized product design and production, with its cost-effectiveness, design flexibility, and lightweight yet durable results. Spearheaded by industry leaders like [Company Name], aluminum injection molding is poised to reshape diverse sectors, promising a future characterized by enhanced efficiency, improved performance, and sustainable manufacturing practices. As research and development continue to progress, the prospects for this revolutionary method are boundless.
Company News & Blog
Top-quality Injection Molding Parts: Enhancing Manufacturing Processes
FOR IMMEDIATE RELEASE[Company Name] Revolutionizes Injection Molding Parts Industry with Innovative Solutions[CITY, DATE] - [Company Name], a leading provider of injection molding parts, is taking the industry by storm with its groundbreaking innovations and commitment to delivering high-quality, reliable solutions. With a focus on meeting the diverse needs of customers worldwide, the company has gained a reputation for excellence and is poised to shape the future of the injection molding parts market.Injection molding parts play a crucial role in various industries such as automotive, electronics, medical, and consumer goods. They require precision, durability, and flexibility to meet the ever-evolving demands of these sectors. [Company Name] specializes in manufacturing injection molding parts that exceed these expectations, thanks to their cutting-edge technology and commitment to continuous improvement.With state-of-the-art facilities and a highly skilled workforce, [Company Name] is able to provide a wide range of injection molding parts tailored to meet specific customer requirements. Their extensive product portfolio includes but is not limited to plastic components, technical parts, and molds. From intricate designs to large-scale production, they have the expertise and machinery to handle projects of any size or complexity.One of the key factors that set [Company Name] apart from its competitors is their unwavering focus on quality control. They have implemented rigorous testing and inspection procedures throughout the manufacturing process to ensure that every product that leaves their facility meets or exceeds the highest industry standards. By strictly adhering to quality control measures, they have built a reputation for reliability and consistency.The success of [Company Name] can be attributed to their commitment to innovation. They continuously invest in research and development to stay ahead of the curve and introduce groundbreaking solutions that keep the company at the forefront of the industry. By embracing cutting-edge technologies and adopting the latest manufacturing techniques, they have revolutionized the injection molding parts market.In addition to their technical expertise, [Company Name] places great emphasis on providing exceptional customer service. Their team of knowledgeable professionals works closely with clients from the initial concept stage to the final delivery, ensuring a seamless and satisfactory experience. By understanding the unique needs of each customer, [Company Name] is able to deliver customized solutions that maximize efficiency and reduce costs.The impact of [Company Name] extends beyond the products they deliver. As a socially responsible company, they strive to minimize their environmental footprint. By incorporating sustainable practices into their manufacturing processes, such as using eco-friendly materials and optimizing energy consumption, they are actively contributing to a greener future. This commitment to sustainability has earned them accolades and recognition within the industry.Looking ahead, [Company Name] is determined to maintain its position as a leader in the injection molding parts industry. They are investing in expanding their production capabilities and enhancing their product offerings to meet the evolving needs of their customers. With a strong focus on research and development, customer satisfaction, and sustainability, they are poised to shape the future of injection molding parts.About [Company Name]:[Company Name] is a leading provider of injection molding parts, serving a diverse range of industries worldwide. With their commitment to quality, innovation, and customer satisfaction, they have established themselves as a trusted partner in the industry. By constantly pushing the boundaries of what is possible, they are revolutionizing injection molding parts and shaping the future of the market.For more information, please visit [company website] or contact:[Contact Name][Contact Title][Company Name][Phone Number][Email Address]
Discover the Benefits of Sheet Metal Prototypes for Efficient Product Development
Sheet Metal Prototypes Launches Innovative Metal Fabrication Service[Company City, State] - Sheet Metal Prototypes, a leading provider of metal fabrication solutions, is excited to announce the launch of a groundbreaking metal fabrication service that combines cutting-edge technology with extensive expertise in sheet metal production.With over [number of years] years of experience in the industry, Sheet Metal Prototypes has established itself as a trusted partner for businesses looking for high-quality metal components. Their latest innovation showcases their commitment to staying at the forefront of metal fabrication technology.The new metal fabrication service offered by Sheet Metal Prototypes utilizes advanced techniques to produce precise, reliable, and durable metal prototypes. Through computer-aided design (CAD) software and state-of-the-art machinery, their team of skilled engineers can create complex metal parts with unparalleled accuracy."We are thrilled to introduce this cutting-edge metal fabrication service to our clients," said [Company Spokesperson], [Position] at Sheet Metal Prototypes. "Our goal has always been to provide the highest level of quality and precision in our fabricated metal parts, and this new service allows us to take that commitment to the next level."The use of CAD software allows for seamless integration between design and fabrication, eliminating potential errors and ensuring consistent results. Clients can now see virtual renderings of their metal prototypes before they are produced, streamlining the design process and minimizing the risk of costly revisions.Sheet Metal Prototypes' state-of-the-art machinery includes laser cutting systems, CNC punching machines, and press brakes, among others. Each piece of equipment is meticulously maintained to provide optimal performance and enhanced efficiency during the fabrication process.The company's team of highly skilled and experienced engineers collaborates closely with clients, offering extensive knowledge and guidance throughout the metal fabrication process. From design consultations to material selection and prototype development, their expertise ensures that clients receive tailor-made solutions that meet their specific requirements."We understand that every project is unique, and that's why we place great emphasis on close collaboration with our clients," added [Company Spokesperson]. "Our team is dedicated to providing personalized service and delivering high-quality metal prototypes that exceed expectations."Sheet Metal Prototypes' commitment to environmental sustainability is also evident in their metal fabrication service. By employing efficient manufacturing practices and utilizing recyclable materials, they aim to minimize their impact on the environment. The company adheres to strict quality control standards, ensuring that each metal prototype is thoroughly inspected before final delivery.As the demand for precision metal components continues to grow across various industries, Sheet Metal Prototypes remains dedicated to pushing the boundaries of metal fabrication technology. With their innovative service, they have solidified their position as a trusted partner for businesses seeking reliable and high-quality metal prototypes.To learn more about Sheet Metal Prototypes' groundbreaking metal fabrication service, visit their website [website URL] or contact their team at [contact information].About Sheet Metal Prototypes:Sheet Metal Prototypes is a leading provider of metal fabrication solutions, specializing in the production of high-quality metal prototypes. With over [number of years] years of industry experience, their team of skilled engineers combines advanced technology with personalized service to deliver precision-crafted metal parts that meet clients' exact specifications. The company is committed to environmental sustainability and employs eco-friendly practices throughout the fabrication process.
Unlocking the Art of Precision Foam Cutting: A Comprehensive Guide
Precision Foam Cutting Appoints New CEO for Expansion and Continued GrowthPrecision Foam Cutting, a leader in the foam cutting industry, is thrilled to announce the appointment of John Smith as its new CEO. With a proven track record of success in the manufacturing sector, Smith brings a wealth of experience and expertise to the company and will play a pivotal role in driving expansion and continued growth.Founded in 1995, Precision Foam Cutting has established itself as a trusted provider of high-quality foam cutting solutions. Specializing in precision cutting techniques, the company caters to a wide range of industries, including automotive, aerospace, medical, packaging, and beyond. Their precise foam cutting technology and innovative solutions have made them an industry leader, garnering a strong reputation for reliability and excellence.In their pursuit of excellence, Precision Foam Cutting understands the importance of strong leadership. With the appointment of John Smith, an accomplished professional with a deep understanding of manufacturing processes, the company is poised to reach new heights. Smith's vast experience in executive roles, strategic leadership, and business development will be instrumental in driving the company's expansion plans.John Smith's career spans over three decades, during which he has held various leadership positions in the manufacturing sector. Prior to joining Precision Foam Cutting, Smith served as the CEO of a major manufacturing company, where he successfully propelled the organization's growth through strategic initiatives and a focus on operational excellence. His ability to build and lead high-performing teams has consistently delivered outstanding results, making him an ideal fit for Precision Foam Cutting's vision.Speaking on his appointment, John Smith expressed his excitement and commitment to leading Precision Foam Cutting into a new phase of growth. He stated, "Precision Foam Cutting has carved a niche for itself in the foam cutting industry through its relentless pursuit of perfection. I am honored to join this incredible team and contribute towards the company's ambitious expansion plans. Together, we will continue revolutionizing the foam cutting industry, delivering innovative solutions to our customers while maintaining our commitment to quality and excellence."Precision Foam Cutting has been steadily expanding its operations in recent years, catering to an ever-growing customer base. With the appointment of John Smith, the company aims to capitalize on this momentum and further strengthen its market presence. Smith's strategic vision, coupled with Precision Foam Cutting's cutting-edge technology and commitment to customer satisfaction, will undoubtedly drive the company towards achieving new milestones.As the foam cutting industry evolves, Precision Foam Cutting is committed to staying at the forefront of innovation. The company invests heavily in research and development, continually exploring new technologies and techniques to enhance their foam cutting solutions. This dedication to innovation ensures that Precision Foam Cutting remains a trusted partner for cutting-edge solutions, catering to the evolving needs of its diverse clientele.In conclusion, Precision Foam Cutting's appointment of John Smith as CEO is a significant milestone in the company's journey. With Smith at the helm, the company is poised for continued growth, expansion, and innovation in the foam cutting industry. Together, Precision Foam Cutting and John Smith will lead the way in delivering cutting-edge foam cutting solutions and solidifying the company's position as an industry leader.
Chinese Brass Parts Manufacturers: A Deep Dive into the CNC Industry
Title: Chinese CNC Brass Parts Manufacturers: Revolutionizing Precision EngineeringIntroduction:In today's era of advanced technology and digitization, the demand for precision engineering components has witnessed a significant surge. Chinese companies have notably emerged as key players in the global manufacturing industry. Among the forefront leaders are China's reputable CNC brass parts manufacturers. These companies are revolutionizing precision engineering with their cutting-edge technology and superior quality products.A Booming Industry:China’s CNC brass parts manufacturing industry has experienced remarkable growth over the years. This growth can be attributed to several factors such as technological advancements, government support, and a skilled workforce. With their state-of-the-art facilities and adherence to stringent quality standards, these manufacturers have gained recognition as trustworthy suppliers to various sectors including automotive, aerospace, electronics, telecommunications, and many more.Technological Advancements:The CNC brass parts manufacturers in China have made substantial investments in advanced machinery and equipment. They meticulously integrate the latest technologies such as computer numerical control (CNC) machining, precision grinding, and automated assembly lines into their manufacturing processes. This enables them to produce high-quality brass components with unparalleled precision and accuracy, ensuring a seamless fitment and optimal performance in end products.Quality is Paramount:China's CNC brass parts manufacturers have always maintained a commitment to delivering superior quality products. These manufacturers follow rigorous quality control processes at every stage of production. From meticulous raw material selection to precision machining and stringent inspections, every step is carried out with utmost precision. In addition, they adhere to international standards such as ISO 9001, ensuring that the final products meet and exceed customer expectations in terms of durability, reliability, and functionality.Customization and Flexibility:Chinese CNC brass parts manufacturers understand the diverse and ever-changing requirements of their global clientele. They offer a wide range of customization options, enabling customers to tailor the components to suit their specific needs. From intricate designs to complex geometries, these manufacturers possess the technical expertise to transform customers' requirements into tangible products. This flexibility has earned them a reputation for being reliable solution providers, ensuring customer satisfaction across various industries.Competitive Pricing and Timely Delivery:One of the key advantages of working with Chinese CNC brass parts manufacturers is their competitive pricing without compromising on quality. The combination of affordable manufacturing costs and economies of scale allows them to offer cost-effective solutions to customers. Moreover, these manufacturers have efficient supply chains and logistics networks, ensuring prompt delivery of orders across the globe. Their ability to meet tight deadlines has made them sought-after partners for both small-scale projects and large-scale production requirements.Global Reach and Export Excellence:Chinese CNC brass parts manufacturers have expanded their market reach to cater to the demands of a global customer base. With a focus on export excellence, they have successfully penetrated international markets, including North America, Europe, Asia-Pacific, and the Middle East. These manufacturers leverage their extensive experience and industry knowledge to adapt to the varying regulations and demands of different regions, firmly establishing themselves as trusted suppliers worldwide.Conclusion:China’s CNC brass parts manufacturers have emerged as frontrunners in the global manufacturing industry, leveraging cutting-edge technology, superior quality, customization options, competitive pricing, and timely delivery. Their commitment to precision engineering and their ability to cater to a diverse range of industry requirements have positioned them as reliable partners for companies worldwide. With continued innovation and customer-centricity at the core of their operations, it is evident that these manufacturers will continue to shape the landscape of precision engineering in the years to come.
Exploring the Benefits of Aluminum Injection Molding in Today's Manufacturing Industry
[Assistant]Title: Revolutionizing Manufacturing: Aluminum Injection Molding Sets New Industry StandardsIntroduction:Innovation continues to be the driving force behind advancements in the manufacturing industry. Among the latest breakthroughs is the revolutionary technique of aluminum injection molding. This cutting-edge manufacturing process has the potential to reshape various sectors by providing unique advantages such as cost-effectiveness, increased design flexibility, and enhanced production efficiency. In this article, we delve into the details of aluminum injection molding, exploring its benefits, applications, and the promising future it holds.Understanding Aluminum Injection Molding:Aluminum injection molding is an advanced manufacturing technique that combines the versatility of plastic injection molding with lightweight and durable aluminum materials. This process involves injecting molten aluminum under high pressure into complex and intricate molds, allowing for the creation of intricate parts and components with exceptional precision. The process takes advantage of the desirable properties of aluminum, including its high strength-to-weight ratio, corrosion resistance, and excellent thermal conductivity.The Company's Role:The trailblazers in aluminum injection molding technology, [Company Name], have been at the forefront of the industry, leading in research, development, and implementation of this groundbreaking method. Their extensive experience and cutting-edge facilities have enabled them to refine and perfect the aluminum injection molding process, making it highly efficient and adaptable to various manufacturing requirements. The company's dedication to continuous innovation has positioned them as a driving force behind the widespread adoption of aluminum injection molding.Applications and Industries Transformed:The advent of aluminum injection molding has had a transformative impact across numerous industries, offering a wide range of applications and benefits. In the automotive sector, lightweight aluminum components produced through this process have revolutionized vehicle design, leading to improved fuel efficiency, better performance, and enhanced safety. Similarly, aerospace manufacturers are benefiting from the lightweight properties of aluminum injection-molded parts, resulting in reduced fuel consumption and increased payload capabilities.Electronics and telecommunications industries can leverage the design flexibility of aluminum injection molding to create intricate and high-performance electronic enclosures and housings. The process also allows for the integration of additional features, such as heat sinks, resulting in improved thermal management and extended device lifespans.The medical field is yet another sector where aluminum injection molding can make a profound impact. The ability to produce complex and sterile medical devices and implants made from lightweight yet durable aluminum materials opens new possibilities for enhanced patient care, improved surgical outcomes, and cost-effective medical solutions.Benefits Driving Adoption:The widespread adoption of aluminum injection molding can be attributed to the numerous benefits it offers. One of the most significant advantages is the cost-effectiveness of the process. By utilizing aluminum materials, which are relatively inexpensive, manufacturers can produce lightweight yet strong components without breaking the bank. This affordability extends to the tooling process as well, as aluminum molds are generally less costly than traditional injection molding molds.Moreover, aluminum injection molding enables manufacturers to achieve intricate and precise designs that were previously unattainable. The ability to create complex geometries with exceptional accuracy allows for the integration of multiple functions into a single part, reducing assembly time and enhancing overall product performance.Furthermore, the lightweight nature of aluminum components facilitates transportation and logistics, ultimately reducing costs and environmental impact. Aluminum's corrosion resistance properties also ensure long-lasting durability, making it an ideal choice for applications exposed to harsh environments or demanding conditions.The Path Towards a Promising Future:As aluminum injection molding continues to gain traction, researchers and manufacturers are working collaboratively to push its boundaries further. The ongoing advancement of this technology aims to enhance process efficiency, minimize cycle times, and explore possibilities for new alloy variants. Additionally, efforts are being made to streamline post-processing techniques such as surface treatments and finishing processes to ensure the highest quality standards.Industry experts predict that aluminum injection molding will play a pivotal role in the wider adoption of electric vehicles, thanks to the efficiency gains and material advantages it offers. Furthermore, as sustainability and lightweighting remain key focus areas for many industries, aluminum injection molding will likely continue to grow, revolutionizing diverse sectors such as consumer electronics, renewable energy, and industrial manufacturing.Conclusion:Aluminum injection molding represents a transformative leap in the manufacturing industry. This innovative technique has revolutionized product design and production, with its cost-effectiveness, design flexibility, and lightweight yet durable results. Spearheaded by industry leaders like [Company Name], aluminum injection molding is poised to reshape diverse sectors, promising a future characterized by enhanced efficiency, improved performance, and sustainable manufacturing practices. As research and development continue to progress, the prospects for this revolutionary method are boundless.
Understanding the Importance and Applications of Injection Molds
[Company Name] Introduces Advanced Injection Molding Technology for Enhanced Efficiency and Quality[City, Date] - [Company Name], a leading provider of advanced manufacturing solutions, has unveiled their latest innovation in injection molding technology - Pla Injection Molds. This groundbreaking development promises to revolutionize the manufacturing industry by offering enhanced efficiency and superior quality in plastic production.Injection molding is a widely-used manufacturing process for the production of plastic parts in various industries, including automotive, electronics, medical, and consumer products. [Company Name] has been at the forefront of developing cutting-edge technologies to improve this process and meet the evolving demands of their customers.The newly introduced Pla Injection Molds are an exciting addition to their extensive portfolio of advanced manufacturing solutions. By combining innovative design features with high-quality materials, [Company Name] has created molds that offer unparalleled precision and durability.One of the key features of Pla Injection Molds is their use of polylactic acid (PLA), a biodegradable and bioactive thermoplastic. PLA is derived from renewable resources such as corn starch or sugarcane and is gaining popularity as a sustainable alternative to traditional plastics. By incorporating PLA into their injection molds, [Company Name] is showcasing their commitment to environmentally conscious manufacturing practices.The use of PLA in injection molding not only contributes to a greener planet but also offers numerous performance advantages. PLA molds exhibit excellent dimensional stability, ensuring consistent and accurate production of plastic parts. This is critical, especially in industries where precision and reliability are paramount.In addition to superior dimensional stability, PLA Injection Molds also provide exceptional heat resistance and surface finish. This extends the lifespan of the molds, reducing maintenance costs and increasing overall production efficiency. Moreover, the bioactive properties of PLA prevent bacterial growth on the mold surface, enhancing the cleanliness and hygiene of the manufacturing process.[Company Name] understands the importance of customization and versatility in modern manufacturing, and the Pla Injection Molds are designed to meet these requirements. The molds can be easily tailored to accommodate a wide range of materials, designs, and product specifications. This flexibility allows their customers to produce a diverse array of plastic parts, ensuring their products remain at the forefront of their respective markets."We are thrilled to introduce Pla Injection Molds as the latest addition to our ever-expanding range of advanced manufacturing solutions," said [Company Name]'s CEO. "At [Company Name], we strive to deliver the highest quality products while being mindful of our environmental impact. The Pla Injection Molds perfectly embody these values, providing our customers with a sustainable and efficient solution for their manufacturing needs."With over [XX] years of experience in the industry, [Company Name] has built a solid reputation for delivering innovative, reliable, and cost-effective manufacturing solutions. Their unmatched expertise, combined with the advanced features of Pla Injection Molds, positions [Company Name] as a top-choice partner for businesses seeking to enhance their manufacturing processes.For more information about Pla Injection Molds and other advanced manufacturing solutions offered by [Company Name], visit their official website at [website].About [Company Name]:[Company Name] is a leading provider of advanced manufacturing solutions, specializing in injection molding, CNC machining, and additive manufacturing. With a commitment to innovation and customer satisfaction, [Company Name] has established a strong presence in various industries, including automotive, electronics, medical, and consumer products. Their team of experts works closely with clients to deliver tailored solutions that meet their specific requirements, ensuring superior product quality and efficiency.###
Unlocking the Potential of Rapid Tooling Injection Molding for Advanced Manufacturing
Title: Advancements in Rapid Tooling Injection Molding Streamline Manufacturing ProcessesIntroduction:In recent years, the manufacturing industry has witnessed remarkable advancements in technology, with rapid tooling injection molding emerging as a cutting-edge technique. This process allows for the production of high-quality prototype parts, reducing lead times and costs significantly. One prominent player in this field, [Company Name], has taken a leap forward with their innovative solutions and expertise in this domain. This article aims to delve into the world of rapid tooling injection molding and shed light on how [Company Name] is revolutionizing manufacturing processes.Rapid Tooling Injection Molding:Rapid tooling injection molding, also known as RTIM, is a manufacturing technique that combines traditional injection molding methods with rapid prototyping technologies. This process involves the production of tooling inserts using additive manufacturing techniques or subtractive processes like CNC machining. These inserts are then integrated into injection molds, enabling the mass production of high-quality plastic parts in a short period.By significantly reducing lead times, RTIM allows manufacturers to bring products to market faster, giving them a competitive edge. Additionally, this technique eliminates the need for expensive and time-consuming metal tooling, making it an attractive option for small-scale production runs, prototypes, and low-volume manufacturing.[Company Name]'s Innovative Solutions:[Company Name] is a leading player in the field of rapid tooling injection molding. With their expertise and dedication to innovation, they have developed a range of solutions that have wide-ranging applications across industries.1. Advanced Material Selection:[Company Name] understands the importance of selecting the right materials for each project. They offer a wide variety of thermoplastics and specialty materials, ensuring the utmost precision, durability, and functional performance in the final product. By leveraging their materials expertise, they can cater to diverse customer requirements, from medical-grade parts to aerospace components.2. Design Optimization:One of the significant advantages of rapid tooling injection molding is the ability to optimize designs quickly. [Company Name] employs design engineers who work closely with clients to enhance the manufacturability of their products. By utilizing advanced simulation techniques, they identify potential design flaws early in the process, reducing iterations and achieving higher quality end products efficiently.3. Automation and Robotics:To further enhance efficiency, [Company Name] leverages automation and robotics in their manufacturing processes. This integration streamlines operations, reducing human error and enhancing overall production output. The company's investment in cutting-edge automation technology ensures consistent, high-quality parts while maintaining cost-effectiveness.4. Quality Control and Testing:[Company Name] places utmost importance on quality control and testing throughout the manufacturing process. By employing stringent quality assurance protocols, including dimensional analysis, functionality testing, and surface finish inspections, they ensure that the final products meet or exceed industry standards. This commitment to quality has earned them a solid reputation among their clientele.Conclusion:Rapid tooling injection molding has revolutionized the manufacturing industry by enabling fast, cost-effective production of high-quality plastic parts. [Company Name], with its expertise and innovative solutions, has emerged as a key player in this field. Their commitment to material selection, design optimization, strategic automation, and rigorous quality control makes them an industry leader capable of meeting diverse customer requirements. As technology continues to evolve, it is exciting to witness the transformative impact rapid tooling injection molding, along with companies like [Company Name], is having on the manufacturing industry.
Discover the Latest Small High Precision Lathe for Enhanced Precision
Small High Precision Lathe Revolutionizes Machining: A Game Changer for Manufacturing IndustriesIn today's rapidly evolving manufacturing landscape, precision and efficiency are of paramount importance. With the introduction of the groundbreaking Small High Precision Lathe, manufacturing companies around the world are set to experience a revolutionary change in their machining processes. Although we cannot mention the brand name, this cutting-edge technology promises to deliver exceptional results, ensuring heightened precision, unparalleled productivity, and reduced production time.Manufacturing has always been a complex and challenging process, requiring meticulous attention to detail and the use of advanced machinery. The Small High Precision Lathe, with its innovative features and capabilities, is set to enhance the performance of machining operations across various industries, including aerospace, automotive, and medical.With a compact and ergonomic design, this lathe utilizes state-of-the-art technology to achieve extraordinary precision. Its advanced control system, combined with specialized software, enables users to execute intricate machining tasks with ease and accuracy. The lathe's high spindle speed and exceptional torque ensure that even the most complex components can be machined with precision, meeting the stringent quality standards of modern industries.Beyond its impressive precision, the Small High Precision Lathe also offers remarkable versatility. Its adjustable tooling options and multiple-axis functionalities allow for a wide range of machining operations, from turning and facing to threading and knurling. The lathe's automatic tool change system further streamlines the manufacturing process, reducing downtime and boosting overall productivity.Companies that have already integrated this technology into their manufacturing processes have reported significant improvements in their operational efficiency. The Small High Precision Lathe's fast setup and programming capabilities enable rapid production, resulting in shorter lead times and increased output. Furthermore, the lathe's ability to handle both small and large batches of components makes it an invaluable asset for manufacturers of various scales.The implementation of this cutting-edge lathe technology also contributes to a greener and more sustainable manufacturing environment. Its energy-efficient design, coupled with optimized machining processes, reduces power consumption and promotes responsible production practices. As manufacturers strive to meet environmental regulations and reduce their carbon footprint, the Small High Precision Lathe aligns perfectly with their sustainability goals.While the Small High Precision Lathe delivers exceptional performance on its own, it also integrates seamlessly into existing manufacturing systems. Its compatibility with computer-aided design (CAD) and computer-aided manufacturing (CAM) software allows for efficient data exchange, ensuring a smooth transition from design to production. Additionally, the lathe's remote monitoring and diagnostic features enable real-time troubleshooting, reducing maintenance costs and increasing equipment uptime.As the manufacturing industry continues to evolve, the demand for higher precision and efficiency will only intensify. The Small High Precision Lathe represents a significant leap forward in machining technology, addressing these demands head-on. Its sophisticated features, exceptional precision, and user-friendly interface make it an indispensable tool for manufacturers worldwide.With this cutting-edge technology, manufacturers can expect reduced costs, increased productivity, and improved product quality. The Small High Precision Lathe not only meets these expectations but also sets new standards for the industry as a whole. As manufacturing companies embrace this revolutionary technology, they are poised to gain a competitive edge in a rapidly evolving global market.In conclusion, the Small High Precision Lathe revolutionizes the manufacturing landscape, offering a game-changing solution to the precision machining challenges faced by industries today. By combining state-of-the-art technology, unrivaled precision, and unmatched versatility, this lathe promises to propel manufacturing companies into a new era of efficiency and productivity. With its compact design, advanced control system, and eco-friendly features, the Small High Precision Lathe is set to redefine the future of machining.
Rewriting the SEO title without the brand name: "Effective Plastic Injection Tooling: Unveiling the Latest Innovations and Techniques
Plastic Injection Tooling: Revolutionizing Manufacturing ProcessesIn today's highly advanced and technologically driven world, plastic injection tooling plays a vital role in revolutionizing manufacturing processes. By incorporating the latest cutting-edge technologies and innovative design practices, this vital tooling equipment has enabled companies across various industries to produce high-quality plastic components efficiently and cost-effectively.Plastic injection tooling, also known as injection molds or dies, is a primary component of the injection molding process. It is a custom-made precision tool that is used to shape molten plastic into a desired form, creating a wide array of products such as automotive parts, consumer electronics, medical devices, and household items.The process starts with the design and engineering of the injection mold. This step involves careful analysis of the product requirements and specifications to create a mold design that ensures optimal functionality and durability. Advanced computer-aided design (CAD) software is used to model the mold, taking into account factors such as material flow, cooling channels, and ejection methods.Once the design is finalized, modern manufacturing techniques such as computer numerical control (CNC) machining and electrical discharge machining (EDM) are employed to fabricate the injection mold with extreme precision. The use of high-quality materials and state-of-the-art equipment ensures that the mold is durable, long-lasting, and capable of producing consistent and error-free parts.Plastic injection tooling offers several advantages over other manufacturing processes. Firstly, it allows for mass production of complex parts with intricate geometries that would otherwise be impossible to manufacture using traditional methods. This high degree of design flexibility has enabled companies to create innovative and aesthetically pleasing products that cater to consumer demand.Secondly, plastic injection tooling significantly reduces production time and costs. The automation of the injection molding process ensures fast and efficient production cycles, minimizing labor costs and increasing overall productivity. Additionally, the ability to manufacture large quantities of parts in a short period eliminates the need for additional manufacturing steps and saves valuable time.Moreover, plastic injection tooling allows for tight tolerances and excellent surface finishes, providing high-quality parts that meet the stringent standards of various industries. This precision ensures that the parts function as intended, enhancing product performance and customer satisfaction.In recent years, advancements in plastic injection tooling have further accelerated the manufacturing process. The integration of technologies like 3D printing and simulation software has revolutionized the design and prototyping phases, facilitating rapid iteration and reducing time-to-market. This has enabled companies to swiftly adapt to market demands and stay ahead of the competition.One company at the forefront of plastic injection tooling innovation is {}. With over {} years of experience, they have established themselves as a reliable and trusted provider of injection molds. Their team of skilled engineers and technicians leverage the latest technologies to design and manufacture molds that meet the highest industry standards.As a customer-oriented company, {} strives to deliver exceptional quality and customer service. They work closely with their clients during every stage of the project, from initial concept to final production, to ensure that their specific requirements are met. Additionally, their emphasis on continuous improvement and investment in research and development enable them to offer cutting-edge solutions that drive efficiency and profitability.In conclusion, plastic injection tooling has revolutionized manufacturing processes by enabling companies to produce high-quality plastic components with unparalleled design flexibility, precision, and cost efficiency. With innovative technologies and companies like {} leading the way, the future of plastic injection tooling looks promising, offering endless possibilities for product development and advancement across various industries.
High-Quality CNC Precision Turned Parts: An Essential Guide for Machining Success
Title: Advancements in CNC Precision Turned Parts Revolutionize Manufacturing ProcessesIntroduction:In today's rapidly changing technological landscape, precision engineering plays a critical role in driving innovation and efficiency across various industries. CNC Precision Turned Parts, offered by leading companies in the sector, have emerged as a game-changing solution in manufacturing processes. By leveraging the power of computer numerical control (CNC) technology, these parts offer unparalleled accuracy, reliability, and versatility, revolutionizing the way components are produced.Body: 1. Understanding CNC Precision Turned Parts:CNC Precision Turned Parts refer to intricately designed components manufactured using CNC turning machines. These machines utilize computer-controlled movements to produce parts with exceptionally high accuracy and repeatability. By utilizing a combination of rotating cutting tools and computer-controlled movements, CNC machining ensures precise dimensions, tolerances, and surface finishes, resulting in superior quality components.2. Advantages of CNC Precision Turned Parts:a) Enhanced Precision and Accuracy: The integration of CNC technology eliminates human error and enables the production of parts with microscopic tolerances, ensuring the highest level of precision possible.b) Efficiency and Speed: CNC machining processes significantly reduce production time, allowing for faster turnaround and increased productivity.c) Versatility: CNC turning machines are capable of manufacturing complex and intricate components from a wide range of materials, including metal alloys, plastics, and composites.d) Cost-effective Manufacturing: CNC Precision Turned Parts streamline production workflows, reducing labor costs and material waste while improving overall operational efficiency.e) Consistency and Reproducibility: CNC machining guarantees consistent quality and uniformity across multiple batches or order quantities, meeting stringent industry standards.3. Applications across Industries:CNC Precision Turned Parts have found applications across a wide array of industries, including:- Aerospace: CNC turned parts are crucial for manufacturing aircraft components, such as hydraulic fittings, fuel pumps, valves, and landing gear.- Automotive: Precision turned parts are extensively used in vehicle manufacturing processes, including engine components, transmission systems, and suspension parts.- Electronics: The electronics industry relies on CNC precision turned parts to produce connectors, enclosures, switches, and other intricate components used in various electronic devices.- Medical: CNC machining plays a pivotal role in healthcare, enabling the production of precise medical instruments, implants, prosthetics, and surgical components.- Defense: The defense sector benefits from CNC precision turned parts for creating specialized components used in military equipment, firearms, and armored vehicles.4. Cutting-Edge Technology and Innovation:Leading companies in the CNC Precision Turned Parts space, including (brand name), are continuously investing in cutting-edge technology and innovation to stay at the forefront of the industry:a) Advanced CNC Machinery: Investing in state-of-the-art CNC turning machines that offer multi-axis capabilities, high-speed machining, and advanced tooling options ensures superior product quality and greater manufacturing flexibility.b) Computer-Aided Design (CAD) and Computer-Aided Manufacturing (CAM): Utilizing sophisticated CAD/CAM software enables companies to optimize production processes, reduce errors, and enhance productivity.c) Quality Control and Inspection Systems: Implementing stringent quality control measures, such as advanced metrology equipment and comprehensive inspection protocols, ensure that each CNC precision turned part meets the highest international quality standards.d) Materials Research and Development: Collaborations with material scientists and researchers aid in the development of advanced materials that enhance the performance, durability, and efficiency of CNC precision turned parts.Conclusion:CNC Precision Turned Parts have revolutionized the manufacturing industry, offering unparalleled precision, productivity, and versatility. With advancements in CNC technology and a commitment to innovation, (brand name) and other prominent companies in the sector continue to push the boundaries of what is possible in precision engineering. As these parts become more widely adopted, industries across the board will benefit from increased efficiency, reduced costs, and improved product quality, paving the way for a more advanced and interconnected future.