Innovative Laser Cutting Technology for Polyethylene Foam
By:Admin
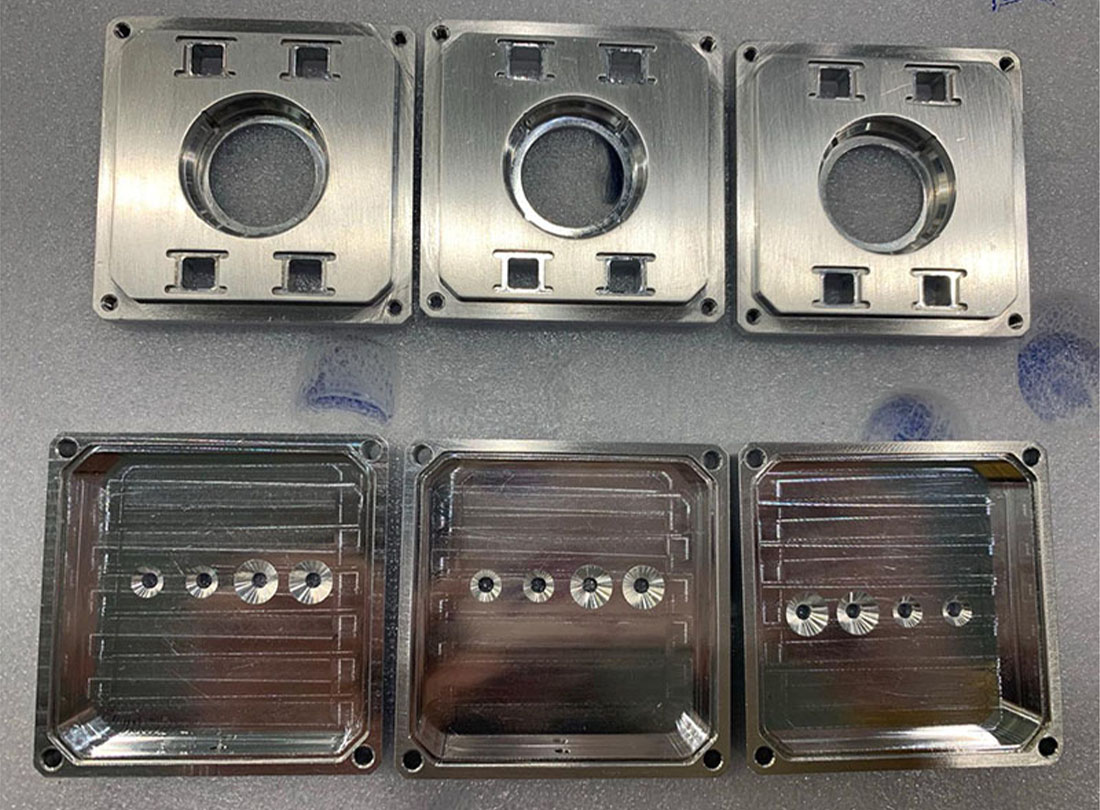
In the world of packaging and retail, the use of polyethylene foam is nothing new. Its cushioning properties make it a popular choice for protecting delicate products during shipping and handling. However, the traditional methods of cutting and shaping polyethylene foam have often been time-consuming and imprecise. That was until the introduction of polyethylene foam laser cutting, a revolutionary technology that is changing the game for packaging manufacturers.
The company behind this groundbreaking innovation is a global leader in laser cutting technology, known for its precision, reliability, and cutting-edge solutions. With a strong focus on research and development, the company has consistently pushed the boundaries of what is possible with laser cutting technology, and the introduction of polyethylene foam laser cutting is just the latest example of their commitment to innovation.
So, what exactly makes polyethylene foam laser cutting so groundbreaking? Unlike traditional cutting methods, which often involve sawing or die-cutting, laser cutting allows for extremely precise and intricate cuts to be made in the foam. This means that manufacturers can create custom-designed foam inserts for packaging that perfectly fit the shape of the product, providing maximum protection and presentation value.
Additionally, laser cutting is a much faster and more efficient process than traditional methods, meaning that manufacturers can produce foam inserts in a fraction of the time. This not only increases productivity but also allows for greater flexibility in meeting customer demands and deadlines.
Furthermore, polyethylene foam laser cutting is a more environmentally friendly option compared to traditional cutting methods. The precision of laser cutting results in minimal waste, as foam pieces can be intricately designed to fit together, leaving very little unused material. This is a significant advantage in an industry that is increasingly focused on sustainability and reducing its environmental impact.
The impact of polyethylene foam laser cutting is already being felt across the packaging industry, with manufacturers adopting this technology to streamline their production processes and deliver higher quality products to their customers. With the ability to create custom-designed foam inserts that offer unmatched protection and presentation, companies using this technology are gaining a competitive edge in the market.
One company that has embraced polyethylene foam laser cutting is (Company name). With a long history of innovation in packaging solutions, (Company name) has quickly recognized the potential of this technology to revolutionize their product offerings. By integrating polyethylene foam laser cutting into their production processes, they have been able to offer their customers a new level of customization and quality in their packaging solutions.
“We are excited to be at the forefront of this cutting-edge technology,” says (Company name) CEO. “Polyethylene foam laser cutting has allowed us to elevate the quality of our packaging products, and we are seeing a tremendous response from our customers who appreciate the level of protection and presentation that our custom-designed foam inserts offer.”
The impact of polyethylene foam laser cutting is not limited to the packaging industry. This technology has the potential to revolutionize a wide range of other applications, from automotive and aerospace to medical and electronics. As manufacturers continue to discover the benefits of laser cutting for polyethylene foam, the possibilities for innovation and improvement in product quality are endless.
As the demand for customized and high-quality packaging solutions continues to grow, it is clear that polyethylene foam laser cutting will play a significant role in shaping the future of the industry. With its unparalleled precision, efficiency, and environmental benefits, this technology is not just a game-changer; it is a clear representation of the potential for innovation to drive progress and improvement in manufacturing processes.
Company News & Blog
High-quality Machining Services for Aerospace Components
Machining Aerospace Components: A Key Player in the Aerospace IndustryWith the increasing demand for air travel and the rapid advancement of technology in the aerospace sector, the need for high-quality precision aerospace components has never been greater. This is where Machining Aerospace Components, a leading aerospace manufacturing company, has been making its mark. Founded in 1985, Machining Aerospace Components has grown to become a trusted and reliable supplier of precision machined components for some of the world's leading aerospace companies. The company's state-of-the-art facilities and cutting-edge technology have enabled it to consistently deliver top-quality aerospace components that meet the demanding specifications of the aerospace industry.Machining Aerospace Components specializes in the production of a wide range of components, including complex structural parts, engine components, and landing gear components. The company's expertise in machining a variety of materials, including aluminum, titanium, and nickel alloys, has positioned it as a key player in the aerospace manufacturing industry.One of the key factors that sets Machining Aerospace Components apart is its commitment to innovation and continuous improvement. The company's team of highly skilled engineers and machinists work tirelessly to develop new machining techniques and processes to enhance the quality and precision of its components. Additionally, Machining Aerospace Components invests heavily in the latest equipment and technology to ensure that it remains at the forefront of aerospace manufacturing.In recent years, Machining Aerospace Components has expanded its capabilities to include additive manufacturing, also known as 3D printing. This innovative technology allows the company to produce highly complex components with intricate geometries that were previously impossible to achieve through traditional machining methods. By embracing additive manufacturing, Machining Aerospace Components has demonstrated its dedication to staying ahead of the curve and meeting the evolving needs of the aerospace industry.Furthermore, Machining Aerospace Components places a strong emphasis on quality control and adherence to industry standards. The company holds several certifications, including AS9100, NADCAP, and ISO 9001, which serve as a testament to its commitment to delivering products of the highest quality. This dedication to quality has earned Machining Aerospace Components a reputation for excellence and reliability among its customers.With its proven track record and commitment to excellence, Machining Aerospace Components has solidified its position as a preferred supplier for aerospace components. The company's unwavering dedication to precision, innovation, and quality has enabled it to establish long-term partnerships with some of the most renowned aerospace companies globally.Looking ahead, Machining Aerospace Components remains focused on expanding its capabilities and continuing to drive innovation in aerospace manufacturing. As the demand for more efficient and advanced aerospace components continues to grow, Machining Aerospace Components is poised to play an instrumental role in shaping the future of the aerospace industry.In conclusion, Machining Aerospace Components has emerged as a leading player in the aerospace manufacturing sector, thanks to its unwavering commitment to precision, innovation, and quality. With its advanced capabilities and dedication to meeting the evolving needs of the aerospace industry, Machining Aerospace Components is well-positioned to continue making significant contributions to the advancement of aerospace technology.
How CNC Machining is Used in Aircraft Part Manufacturing
In recent news, the aerospace industry has seen a significant advancement in the manufacturing of aircraft parts through the utilization of state-of-the-art CNC (Computer Numerical Control) machining technology. This cutting-edge technique has transformed the production process of aircraft components, allowing for higher precision, efficiency, and overall quality.One company at the forefront of this technological revolution is {}. With decades of experience in the aerospace industry, {} has established itself as a leader in the manufacturing and supply of aircraft parts for various commercial and military applications. The company's commitment to innovation and continuous improvement has led to the integration of advanced CNC machining capabilities into its production processes, setting a new standard for excellence in the industry.CNC machining has revolutionized the way aircraft parts are manufactured, offering a level of precision and accuracy that was previously unattainable through traditional manufacturing methods. By using computer-controlled machines and tools, {} is able to create complex and intricate aircraft components with unparalleled precision, resulting in parts that are not only highly reliable but also significantly lighter and more efficient.The use of CNC machining technology also allows for a streamlined production process, reducing lead times and enhancing overall productivity. With the ability to program and automate the machining process, {} can produce aircraft parts at a much faster rate, meeting the increasing demands of the aerospace industry without compromising on quality.Furthermore, CNC machining offers a level of consistency and repeatability that is essential in the aerospace sector. Each aircraft part manufactured using this technology adheres to the exact specifications and requirements, ensuring uniformity and reliability across the board. This level of consistency is crucial in the production of critical aircraft components, where even the smallest deviation can have significant repercussions.In addition to its precision and efficiency, CNC machining also allows {} to work with a wide range of materials, including aluminum, titanium, and composites, further expanding the company's capabilities in meeting the diverse needs of its customers. Whether it's a structural component or a complex engine part, {} has the expertise and technology to deliver high-quality aircraft parts that meet the stringent standards of the aerospace industry.The incorporation of CNC machining technology has not only elevated the production capabilities of {}, but it has also positioned the company as a frontrunner in the aerospace manufacturing sector. With a focus on continuous improvement and innovation, {} remains committed to pushing the boundaries of what is possible in aircraft part manufacturing, setting new benchmarks for quality, precision, and efficiency.As the aerospace industry continues to evolve and demand for more advanced and efficient aircraft components grows, the role of CNC machining in the manufacturing process will only become more significant. With {} leading the way in embracing this technology, the future of aircraft part manufacturing looks to be characterized by unprecedented levels of quality, precision, and reliability.In conclusion, the integration of CNC machining technology into the production processes of {} has brought about a transformative change in the way aircraft parts are manufactured. With a focus on precision, efficiency, and innovation, {} continues to set new standards for excellence in the aerospace industry, solidifying its position as a leading supplier of high-quality aircraft components. As the demand for advanced aerospace technology continues to rise, the role of CNC machining in the manufacturing of aircraft parts will undoubtedly play a crucial role in shaping the future of the industry.
Get the Latest Insights and Updates on Injection Molding Techniques
[Company Name] Revolutionizes the Injection Molding Industry with Cutting-Edge Technology[Location, Date] - [Company Name], a leading provider of innovative manufacturing solutions, is transforming the injection molding industry with their state-of-the-art technology and unwavering commitment to excellence. With a focus on efficiency, quality, and sustainability, [Company Name] is revolutionizing the way products are manufactured through their advanced injection molding processes.Injection molding is a widely used manufacturing process that involves injecting molten material into a mold to create complex shapes with great precision. Traditionally, injection molding has been associated with long cycle times, high costs, and limitations in design flexibility. However, [Company Name] has successfully addressed these challenges and developed innovative solutions that have propelled the industry forward.At the heart of [Company Name]'s success lies their cutting-edge injection molding machine, which boasts enhanced speed, accuracy, and repeatability. This state-of-the-art equipment allows for faster cycle times, increasing production capacity while reducing costs. Additionally, the machine's high precision ensures consistent quality and product integrity, meeting even the most stringent industry standards.Furthermore, [Company Name] has revolutionized the injection molding process by offering an extensive range of materials, including environmentally-friendly options. By incorporating sustainable materials into their manufacturing process, [Company Name] is playing a vital role in reducing the industry's carbon footprint. This commitment to sustainability aligns with the growing consumer demand for eco-conscious products and fosters a greener future for the manufacturing industry.The company's injection molding technology also enables unmatched design flexibility, allowing customers to create intricate designs and incorporate complex features into their products. With the ability to produce parts with varying sizes, shapes, and textures, [Company Name] empowers businesses to differentiate their offerings and stay ahead of their competitors in today's fast-paced marketplace.One of the key advantages of [Company Name]'s injection molding technology lies in its ability to produce parts with exceptional precision, requiring minimal post-production modifications. This not only reduces costs but also accelerates time to market, giving businesses a competitive edge. Moreover, [Company Name]'s commitment to continuous improvement means that their injection molding process is constantly evolving, embracing the latest advancements in technology.In addition to their cutting-edge manufacturing solutions, [Company Name] also offers comprehensive support throughout the entire production cycle. From initial design consultation to final product delivery, their team of experts collaborates closely with customers to ensure that their unique needs and specifications are met. This personalized approach, combined with their industry-leading technology, has earned [Company Name] a reputation for excellence and customer satisfaction.As a testament to their success, [Company Name] has established long-standing partnerships with numerous prestigious clients in industries such as automotive, aerospace, electronics, and consumer goods. Their unwavering commitment to quality, efficiency, and innovation has allowed them to become a trusted partner for companies seeking reliable and high-performing injection molding solutions.Looking ahead, [Company Name] continues to invest in research and development to further advance their injection molding technology. Their dedication to pushing the boundaries of what is possible in the manufacturing industry positions them as a frontrunner in innovation. With a steadfast commitment to sustainability, design flexibility, precision, and customer satisfaction, [Company Name] is set to revolutionize the injection molding industry for years to come.
Ultimate Guide to Plastic Injection Mold Making
Plastic Injection Mold Making is a crucial process in the production of various plastic products. It involves the design and creation of molds that are used to shape and form plastic materials into the desired products. This process requires precision and expertise to ensure that the molds are of high quality and can produce consistent and accurate products.One company that has excelled in the field of Plastic Injection Mold Making is {company name}. With over 20 years of experience in the industry, {company name} has established itself as a leading provider of mold making services. The company specializes in creating custom molds for a wide range of industries, including automotive, medical, consumer goods, and more.{company name} takes pride in its ability to deliver high-quality molds that meet the unique requirements of each client. The company has a team of skilled engineers and designers who work closely with clients to understand their specific needs and develop customized solutions. From the initial design concept to the final production, {company name} ensures that every step of the mold making process is carried out with precision and attention to detail.One of the key factors that sets {company name} apart from its competitors is its commitment to innovation and technology. The company invests in state-of-the-art equipment and utilizes the latest software and tools to streamline the mold making process. This not only allows for greater precision and accuracy in mold design, but also enables {company name} to deliver molds in a shorter timeframe, helping clients to bring their products to market faster.In addition to its technical capabilities, {company name} also prides itself on its dedication to quality and customer satisfaction. The company follows strict quality control measures to ensure that every mold meets the highest standards. This includes thorough testing and inspection of the molds to guarantee their performance and durability.Furthermore, {company name} places a strong emphasis on building long-term partnerships with its clients. The company works collaboratively with clients throughout the mold making process, providing regular updates and seeking feedback to ensure that the final product meets their expectations. {company name}’s commitment to customer service and support has earned it a reputation as a reliable and trustworthy partner in the industry.With its extensive experience, technical expertise, and dedication to quality, {company name} has become a go-to source for Plastic Injection Mold Making. The company has successfully delivered custom molds for a wide range of applications, helping clients to bring their innovative products to market.Looking ahead, {company name} remains focused on driving innovation and excellence in Plastic Injection Mold Making. The company continues to invest in new technologies and processes to further enhance its capabilities and deliver even greater value to its clients. With a strong track record of success and a commitment to continuous improvement, {company name} is well-positioned to remain a leader in the field of mold making for years to come.
Affordable Low Volume Plastic Molding Services for Your Business Needs
Low volume plastic molding is a specialized manufacturing process that is ideal for producing small quantities of plastic parts with complex designs. This process is perfect for businesses looking to test new designs, produce prototypes, or create custom parts without the need for large production runs.{Company Name} is a leading manufacturer in the field of low volume plastic molding. With state-of-the-art technology and a team of skilled engineers, they offer high-quality plastic molding solutions for a wide range of industries. Their focus on innovation and customer satisfaction has made them a trusted partner for businesses looking for low volume plastic molding services.The process of low volume plastic molding involves using molds to shape molten plastic material into the desired part. This method is cost-effective for producing small quantities of plastic parts, as it eliminates the need for expensive tooling and large production runs. {Company Name} has invested in advanced machinery and equipment to ensure precise and efficient plastic molding processes, allowing them to meet the unique needs of their customers.One of the key advantages of low volume plastic molding is the ability to quickly produce prototypes and test new designs. This allows businesses to refine their products and bring them to market faster, saving time and money in the development process. {Company Name} has the expertise and resources to assist their clients in the design and prototyping stages, helping them achieve their goals efficiently.Additionally, low volume plastic molding is an ideal option for businesses that require custom parts or components. {Company Name}'s ability to produce small quantities of highly customized plastic parts makes them a valuable partner for businesses in various industries, including automotive, consumer goods, electronics, and more. Their dedication to meeting the unique needs of their clients sets them apart in the field of low volume plastic molding.In addition to their expertise in low volume plastic molding, {Company Name} prides itself on its commitment to quality and customer satisfaction. They adhere to strict quality control standards throughout the manufacturing process to ensure that every plastic part meets the highest standards of precision and durability. This dedication to quality has earned them a reputation as a reliable and trusted partner for businesses seeking low volume plastic molding solutions.As the demand for low volume plastic molding continues to grow, {Company Name} remains at the forefront of the industry with their innovative approach and dedication to excellence. Their ability to produce high-quality plastic parts in small quantities, combined with their commitment to customer satisfaction, makes them a leader in the field of low volume plastic molding.Businesses looking for a reliable and experienced partner for low volume plastic molding can trust {Company Name} to deliver exceptional results. With their state-of-the-art technology, skilled engineers, and dedication to quality, they are well-equipped to meet the unique needs of their clients and provide high-quality plastic molding solutions for a wide range of industries.
Ultimate Guide to Bioplastics Injection Molding: Everything You Need to Know
Bioplastics Injection Molding is becoming an increasingly popular choice for businesses looking to reduce their environmental impact. This innovative process allows manufacturers to produce high-quality plastic products using biodegradable and renewable materials, making it a sustainable alternative to traditional petroleum-based plastics. The technology is changing the landscape of the injection molding industry, and one company at the forefront of this movement is {}.{} is a leading provider of bioplastics injection molding solutions, with a strong focus on sustainability and environmental responsibility. The company has been a pioneer in the development and adoption of bioplastics, working with a wide range of industries to help them transition to more eco-friendly manufacturing processes. With a state-of-the-art facility and a team of experienced professionals, {} has established itself as a reliable partner for businesses looking to make the switch to bioplastics injection molding.The process of bioplastics injection molding involves using biodegradable and renewable materials, such as PLA (polylactic acid) and PHA (polyhydroxyalkanoates), to produce plastic products. These materials are derived from natural sources like corn, sugarcane, and cassava, making them a sustainable and environmentally friendly alternative to traditional plastics. Bioplastics injection molding offers the same level of performance and durability as petroleum-based plastics, while also being compostable and reducing reliance on finite fossil fuels.One of the key advantages of bioplastics injection molding is its positive impact on the environment. Traditional petroleum-based plastics are a major contributor to pollution and the depletion of natural resources, making the switch to bioplastics an important step towards a more sustainable future. By using renewable materials and reducing the carbon footprint of production, businesses can minimize their environmental impact and contribute to the global effort to combat climate change.In addition to its environmental benefits, bioplastics injection molding also offers economic advantages for businesses. As the demand for sustainable products continues to grow, companies that invest in bioplastics manufacturing are well-positioned to meet consumer preferences and stay ahead of regulatory requirements. By adopting bioplastics injection molding, businesses can enhance their brand image, gain a competitive edge, and tap into new market opportunities while reducing their long-term costs.{} has been instrumental in helping businesses harness the benefits of bioplastics injection molding. The company's expertise in material selection, mold design, and process optimization has enabled clients to seamlessly integrate bioplastics into their manufacturing operations. With a strong commitment to quality, innovation, and customer satisfaction, {} provides end-to-end solutions that meet the unique needs of each client and ensure the successful implementation of bioplastics injection molding.As part of its dedication to sustainability, {} also emphasizes the importance of responsible waste management. The company has implemented initiatives to minimize waste and recycle materials wherever possible, further reducing the environmental impact of its operations. By adhering to strict environmental standards and promoting sustainable practices, {} sets a valuable example for the industry and encourages others to follow suit.In conclusion, bioplastics injection molding is revolutionizing the way plastic products are manufactured, offering a sustainable and eco-friendly alternative to traditional plastics. With its expertise, innovative approach, and commitment to sustainability, {} is driving the adoption of bioplastics injection molding and helping businesses make a positive impact on the environment. As the demand for sustainable solutions continues to grow, the company is well-positioned to lead the industry towards a more sustainable and prosperous future.
High-Quality Sheet Metal Fabrication Service for Custom Projects
Custom Sheet Metal Fabrication ServiceSheet metal fabrication is a process that involves shaping, cutting, and assembling metal sheets to create a wide range of products. Whether it's for automotive, aerospace, construction, or any other industry, custom sheet metal fabrication is a crucial service that requires precision, expertise, and attention to detail. With the increasing demand for custom-made metal products in various industries, the need for a reliable and efficient sheet metal fabrication service has never been greater.Fortunately, {Company Name} provides high-quality custom sheet metal fabrication services tailored to the specific needs of its clients. With its state-of-the-art equipment, skilled professionals, and commitment to excellence, {Company Name} has established itself as a leader in the sheet metal fabrication industry.{Company Name} offers a wide range of custom sheet metal fabrication services, including laser cutting, bending, welding, and assembly. The company's team of experts is equipped with the knowledge and expertise to work with various metals, including stainless steel, aluminum, copper, and more. Whether it's a small prototype or a large-scale production, {Company Name} has the capabilities to deliver top-notch sheet metal fabrication solutions.One of the key factors that set {Company Name} apart from its competitors is its dedication to customer satisfaction. The company works closely with its clients to understand their unique requirements and deliver tailored solutions that meet or exceed their expectations. With a focus on quality, efficiency, and innovation, {Company Name} strives to be the go-to partner for all custom sheet metal fabrication needs.In addition to its commitment to excellence, {Company Name} is also dedicated to sustainability and environmental responsibility. The company uses cutting-edge technologies and processes to minimize waste, reduce energy consumption, and maximize efficiency in its operations. By prioritizing sustainability, {Company Name} not only benefits the environment but also ensures cost-effective and eco-friendly solutions for its clients.Furthermore, {Company Name} takes pride in its ability to meet tight deadlines and deliver projects on time without compromising quality. The company understands the importance of timeliness in the fast-paced industries it serves and has built a reputation for its reliability and efficiency in delivering custom sheet metal fabrication solutions.With its extensive experience, innovative approach, and unwavering commitment to excellence, {Company Name} has earned the trust and loyalty of its clients across various industries. Whether it's for a new product development, custom component fabrication, or any other sheet metal needs, {Company Name} is the preferred choice for businesses looking for reliable and high-quality solutions.As the demand for custom sheet metal fabrication continues to grow, {Company Name} is well-positioned to meet the evolving needs of its clients. The company remains dedicated to pushing the boundaries of innovation, expanding its capabilities, and delivering cutting-edge solutions that drive success for its clients.In conclusion, custom sheet metal fabrication is a vital service for a wide range of industries, and {Company Name} is at the forefront of providing top-tier solutions for its clients. With its expertise, state-of-the-art facilities, and unwavering commitment to customer satisfaction, {Company Name} is the go-to partner for businesses seeking custom sheet metal fabrication services. Whether it's for prototyping, production, or any other metal fabrication needs, {Company Name} is the trusted choice for excellence, reliability, and innovation.
Benefits of Rapid Prototyping in Product Development
[Rapid Prototype] introduces cutting-edge technology for rapid prototyping[Company Name], a leading innovator in the field of manufacturing and product development, has recently unveiled its latest advancement in rapid prototyping technology. This new technology, called [Rapid Prototype], is set to revolutionize the way prototypes are developed, tested, and refined in a wide range of industries.Rapid prototyping is a crucial step in the product development process, as it allows companies to quickly create physical models of new products and iterate on their designs until they are ready for mass production. Traditionally, the process of creating prototypes has been time-consuming and costly, often involving extensive manual labor and specialized tools. However, [Rapid Prototype] aims to change that by offering a more efficient and cost-effective solution for prototyping.The key innovation behind [Rapid Prototype] is its use of advanced 3D printing technology. By leveraging the power of 3D printing, [Rapid Prototype] is able to rapidly produce highly accurate and detailed prototypes with a level of speed and precision that was previously unattainable. This advancement has the potential to significantly accelerate the product development cycle and reduce the time and resources required to bring new products to market.One of the most exciting aspects of [Rapid Prototype] is its versatility. The technology is capable of producing prototypes from a wide range of materials, including plastics, metals, and ceramics. This means that companies in industries as diverse as automotive, aerospace, consumer electronics, and healthcare can all benefit from the capabilities of [Rapid Prototype].In addition to its technical capabilities, [Rapid Prototype] also offers a user-friendly interface and intuitive software, which streamlines the process of designing and producing prototypes. This allows companies to quickly iterate on their designs and make necessary adjustments with ease, ultimately leading to more refined and market-ready products.[Company Name] has a long history of developing cutting-edge technologies for the manufacturing industry. With a team of experienced engineers and researchers dedicated to pushing the boundaries of what is possible in product development, [Company Name] has consistently been at the forefront of innovation.In unveiling [Rapid Prototype], [Company Name] has once again demonstrated its commitment to driving progress in the field of manufacturing and empowering companies to bring their ideas to life more efficiently and effectively. The introduction of this new technology is expected to have a significant impact on the industry, and [Company Name] is confident that [Rapid Prototype] will be embraced by companies seeking to streamline their product development processes and gain a competitive edge in the market.The launch of [Rapid Prototype] has already generated excitement and interest among industry experts and potential customers, and [Company Name] is poised to capitalize on this momentum by offering demonstrations and consultations to companies interested in incorporating the technology into their product development workflows.As [Rapid Prototype] begins to make its mark on the manufacturing landscape, [Company Name] is already looking ahead to the future and exploring additional ways to enhance its capabilities and offer even more value to its customers.With its powerful combination of cutting-edge technology, strong track record of innovation, and commitment to driving progress in the industry, [Rapid Prototype] is poised to become a game-changer in the world of rapid prototyping, and [Company Name] is proud to be at the forefront of this exciting development.
Ultimate Guide to High Precision CNC Lathe Machines
The high precision CNC lathe, developed by {company name}, is revolutionizing the manufacturing industry with its cutting-edge technology and advanced capabilities. This state-of-the-art machine has been designed to deliver unmatched precision, reliability, and efficiency, setting a new standard for precision manufacturing.{Company name} is a leading manufacturer of advanced CNC machinery and has been at the forefront of innovation in the industry for years. Their commitment to excellence and dedication to pushing the boundaries of what is possible has led to the development of the high precision CNC lathe, a game-changing solution for manufacturers looking to achieve the highest levels of precision and productivity.The high precision CNC lathe is equipped with advanced features and technologies that make it stand out from the competition. With its high-speed spindle and precision tooling, this machine can achieve incredibly tight tolerances and exceptional surface finishes, ensuring that every part produced meets the highest quality standards. Its robust construction and rigid design provide stability and accuracy, even when working with the most challenging materials and complex geometries.One of the key features of the high precision CNC lathe is its advanced control system, which allows for intricate and complex machining operations with ease. The machine is capable of performing a wide range of turning, drilling, and milling processes, giving manufacturers the flexibility to produce a diverse range of components with minimal setup and changeover times. This allows for increased productivity and shorter lead times, ultimately leading to a more efficient and cost-effective manufacturing process.In addition to its impressive performance capabilities, the high precision CNC lathe has been designed with the operator in mind. The machine is equipped with a user-friendly interface and intuitive controls, making it easy to program and operate. Its ergonomic design and accessibility features also contribute to a safer and more comfortable working environment, further enhancing its appeal to manufacturers looking to improve both productivity and employee satisfaction.The high precision CNC lathe is also designed to be highly adaptable, making it suitable for a wide range of applications and industries. Whether it's aerospace, automotive, medical, or any other sector that demands the highest level of precision and reliability, this machine is well-equipped to meet the needs of the most demanding manufacturing environments.{Company name} has a long-standing reputation for providing exceptional service and support to its customers, and the high precision CNC lathe is no exception. The company offers comprehensive training and ongoing technical assistance to ensure that customers can fully maximize the potential of this game-changing machine.With its unmatched precision, advanced capabilities, and user-friendly design, the high precision CNC lathe from {company name} is redefining what is possible in the world of precision manufacturing. This groundbreaking machine is setting a new standard for excellence and is poised to revolutionize the way manufacturers approach precision machining. As the industry continues to evolve, {Company name} remains at the forefront of innovation, driving progress and pushing the boundaries of what is possible with its advanced CNC machinery.
High-Quality Moulded Components for Precision Engineering
Precision Moulded Components (PMC) is a leading manufacturer of high-quality injection moulded components for a wide range of industries. With over 20 years of experience in the industry, PMC has consistently delivered top-notch products to its customers and has built a strong reputation for its commitment to quality and customer satisfaction.The company's state-of-the-art manufacturing facilities are equipped with the latest technology and machinery, allowing PMC to produce complex and precision-engineered components with tight tolerances. This has enabled the company to serve a diverse range of industries, including automotive, aerospace, electronics, and medical devices.One of PMC's key strengths lies in its ability to work closely with its customers to develop customised solutions to meet their specific requirements. The company's team of experienced engineers and designers work collaboratively with clients to understand their needs and develop innovative solutions that are both cost-effective and high-performing.In addition to its customised solutions, PMC also offers a comprehensive range of standard components that are widely used across various industries. These components are manufactured to the same high standards as the customised solutions, ensuring that customers can rely on PMC for all their injection moulding needs.Furthermore, PMC is committed to sustainability and environmental responsibility. The company has implemented various measures to reduce its environmental footprint, including the use of eco-friendly materials and energy-efficient manufacturing processes. This commitment to sustainability has not only helped PMC reduce its impact on the environment but has also positioned the company as a preferred supplier for customers who prioritise sustainability in their supply chain.In recent news, PMC has announced the expansion of its manufacturing facilities to meet the growing demand for its products. The expansion includes the addition of new injection moulding machines and an increase in production capacity. This investment demonstrates PMC's commitment to meeting the needs of its customers and providing them with high-quality components in a timely manner."We are thrilled to announce the expansion of our manufacturing facilities," said John Smith, CEO of PMC. "This expansion will allow us to better serve our customers and meet the growing demand for our products. We are committed to continuous improvement and investing in the latest technology to ensure that we remain at the forefront of the industry."The expansion of PMC's facilities is not only good news for the company but also for its customers. With increased production capacity, PMC will be able to reduce lead times and offer shorter delivery times, enabling its customers to bring their products to market more quickly.In addition to expanding its manufacturing facilities, PMC has also been investing in its workforce. The company provides ongoing training and development opportunities for its employees to ensure that they have the skills and knowledge required to produce top-quality components. By investing in its team, PMC is not only able to maintain its high standards of quality but also foster a culture of innovation and continuous improvement.As PMC continues to grow and expand its capabilities, the company remains focused on its core values of quality, customer satisfaction, and sustainability. With its dedication to excellence and its commitment to meeting the needs of its customers, PMC is well-positioned to continue its success in the injection moulding industry.