Advanced Multi Component Injection Molding for Enhanced Product Development
By:Admin
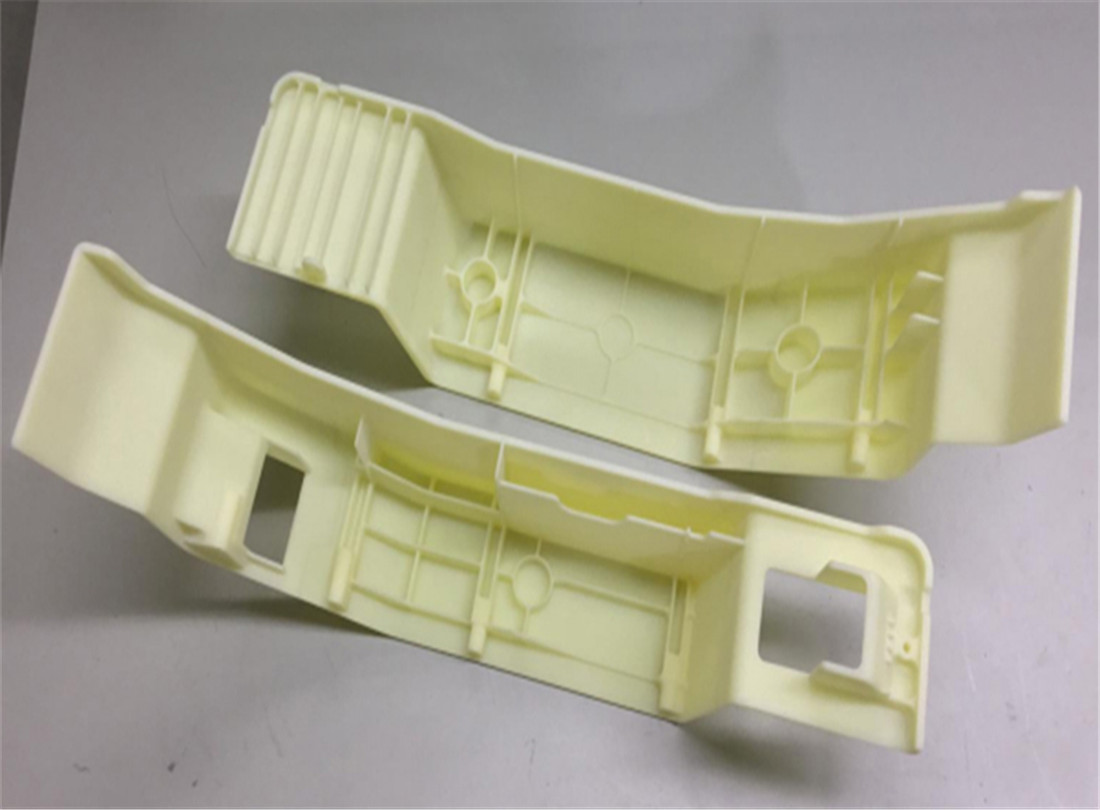
With Multi Component Injection Molding, {Company name} is able to create products with multiple materials and colors in a single molding process. This innovative technique allows for the integration of various functionalities into a single component, reducing the need for additional assembly processes and improving the overall efficiency of the production line. By utilizing this advanced molding technology, {Company name} can offer their customers greater design flexibility and product customization options, ultimately leading to the development of more innovative and marketable products.
{Company name} has invested significantly in state-of-the-art Multi Component Injection Molding machines, leveraging the latest advancements in mold design and material compatibility. This has enabled them to expand their production capabilities and offer a wider range of products to their diverse customer base. In addition, the company has assembled a team of highly skilled engineers and technicians who are proficient in the operation and maintenance of the Multi Component Injection Molding machines, ensuring the consistent delivery of high-quality products.
One of the key advantages of Multi Component Injection Molding is the ability to produce complex and intricate parts with a high degree of precision. {Company name} has leveraged this capability to manufacture a diverse range of products, including automotive components, consumer electronics, medical devices, and household appliances. The company's proficiency in Multi Component Injection Molding has allowed them to meet the stringent quality and performance standards of their customers, leading to high levels of customer satisfaction and long-term partnerships.
Moreover, Multi Component Injection Molding has enabled {Company name} to optimize their production processes, reducing waste and enhancing cost efficiency. By consolidating multiple manufacturing steps into a single molding process, the company has been able to minimize material usage and streamline their production operations. This has not only resulted in cost savings for {Company name}, but has also contributed to their commitment to sustainability and environmental responsibility.
Through the adoption of Multi Component Injection Molding, {Company name} has strengthened their position as a leading manufacturing company in the industry. They have demonstrated their ability to adapt to the evolving needs of the market and provide innovative solutions to their customers. With a focus on continuous improvement and technological advancement, {Company name} is well-equipped to meet the challenges and opportunities of the future, solidifying their status as a preferred partner for complex and sophisticated manufacturing projects.
In conclusion, Multi Component Injection Molding has become a key differentiator for {Company name}, enabling them to expand their capabilities, enhance their product offerings, and improve their operational efficiency. By leveraging this advanced technology, the company is well-positioned to achieve sustained growth and success in the dynamic manufacturing industry. As they continue to invest in innovation and expertise, {Company name} is poised to deliver even greater value to their customers and make a lasting impact on the market.
Company News & Blog
How Insert Moulding Can Enhance Your Product's Design and Functionality
The Insert Moulding industry is booming, and one company that is leading the way in this field is {Company Name}. With their innovative approach and commitment to providing top-notch solutions, they have become a major player in the Insert Moulding market.{Company Name} is a leading manufacturer of Insert Moulding solutions, offering a wide range of products and services to meet the diverse needs of their clients. Their state-of-the-art facilities and cutting-edge technology enable them to produce high-quality moulded parts with precision and efficiency. They have a team of experienced professionals who are dedicated to delivering exceptional results and ensuring customer satisfaction.Insert Moulding is a process that involves the injection of plastic or metal into a pre-formed component, creating a single piece with multiple materials. This technique is widely used in various industries, including automotive, electronics, medical, and consumer goods. {Company Name} has established itself as a go-to source for Insert Moulding solutions, thanks to their expertise and reliability.One of the key factors that set {Company Name} apart from their competitors is their ability to provide customised solutions to meet the specific needs of their clients. They work closely with their customers to understand their requirements and develop tailored Insert Moulding solutions that meet their exact specifications. This level of flexibility and attention to detail has earned them a reputation for excellence in the industry.In addition to their customised solutions, {Company Name} also offers a wide range of standard Insert Moulding products that are designed to meet the needs of various applications. Their extensive catalogue includes a variety of components and parts that are suitable for different industries, ensuring that their clients can find the perfect solution for their specific requirements.With a strong focus on research and development, {Company Name} is constantly pushing the boundaries of Insert Moulding technology. They invest heavily in innovation and are always looking for new ways to improve their processes and products. This commitment to staying ahead of the curve has propelled them to the forefront of the industry, making them a trusted partner for businesses looking for cutting-edge Insert Moulding solutions.Furthermore, {Company Name} is dedicated to sustainability and environmental responsibility. They strive to minimise their impact on the environment by implementing eco-friendly practices and using recyclable materials in their manufacturing processes. This commitment to sustainability has not only helped them reduce their carbon footprint but has also resonated with their environmentally conscious clients.Looking ahead, {Company Name} is poised for continued success in the Insert Moulding market. With their unwavering commitment to quality, innovation, and customer satisfaction, they are well-positioned to meet the evolving needs of their clients and drive the industry forward. As the demand for Insert Moulding solutions continues to grow, {Company Name} is ready to lead the way with their exceptional products and services.In conclusion, {Company Name} is a leading provider of Insert Moulding solutions, offering a diverse range of products and services to meet the needs of their clients. With their focus on innovation, customisation, and sustainability, they have established themselves as a trusted partner in the industry. As they continue to push the boundaries of Insert Moulding technology, {Company Name} is set to maintain their position as a key player in the market for years to come.
High-quality Insert Moulding services for your manufacturing needs
The injection molding industry has been revolutionized by the introduction of Insert Moulding, a cutting-edge technology that has been rapidly adopted by manufacturing companies across the globe. This advanced method allows for the integration of insert parts, such as metal components, into the plastic molding process, resulting in durable and high-quality products.With the rising demand for customized and complex plastic components, Insert Moulding has emerged as a game-changer in the industry. The process involves placing an insert component into the mold cavity and then injecting molten plastic around it to create a single, integrated part. This not only streamlines production processes but also enhances the overall strength and integrity of the final product.{Company}, a leading manufacturer in the injection molding industry, has been at the forefront of implementing Insert Moulding technology into their operations. The company has invested in state-of-the-art machinery and equipment to ensure the seamless integration of insert components, allowing them to offer a wide range of innovative solutions to their clients. Their expert team of engineers and technicians is well-versed in the intricacies of insert molding, enabling them to deliver precise and high-quality parts that meet the stringent requirements of their customers.One of the key advantages of Insert Moulding is the ability to reduce the need for secondary assembly processes, thereby saving time and costs for manufacturers. By incorporating insert components directly into the molding process, {Company} has been able to eliminate the need for additional fastening or bonding methods, resulting in a more efficient and streamlined production cycle. This has had a significant impact on the company's ability to meet tight production deadlines and deliver superior products to their clients.Furthermore, Insert Moulding has opened up new design possibilities for {Company}, allowing them to create complex and intricate parts that were previously unattainable with traditional molding methods. The ability to combine different materials and components has expanded the company's capabilities, enabling them to cater to a broader range of industries and applications. This has positioned {Company} as a versatile and dynamic player in the injection molding market, with the capacity to take on challenging projects and deliver innovative solutions.In addition to its technical advantages, Insert Moulding has also facilitated improvements in the overall quality and performance of {Company}'s products. By integrating insert components directly into the molding process, the company has been able to achieve a higher level of precision and consistency in the production of their parts. This has translated into enhanced durability and reliability for their clients' end products, bolstering {Company}'s reputation as a trusted and dependable partner in the industry.As the demand for customized and complex plastic components continues to grow, {Company} is well-positioned to capitalize on the opportunities offered by Insert Moulding technology. The company's investment in cutting-edge machinery and expertise in insert molding has set them apart as a leader in the field, enabling them to offer innovative solutions that cater to the evolving needs of their clients. With a focus on quality, efficiency, and innovation, {Company} is poised to continue pushing the boundaries of insert molding and delivering superior products to the market.
Custom Molded Plastic Parts: A Key Component in Manufacturing
Pla Molded Parts Company, a leading provider of sustainable packaging solutions, has recently announced the launch of a new line of eco-friendly molded parts. The company, which has been in the business for over two decades, has established itself as a pioneer in the development and production of biodegradable packaging materials. With the increasing global concern for environmental sustainability, Pla Molded Parts Company has been at the forefront of introducing innovative and green solutions to the market.The new line of Pla molded parts is made from polylactic acid, a biodegradable and compostable thermoplastic derived from renewable resources such as corn starch or sugarcane. This material offers the same strength and durability as traditional plastics, making it an ideal choice for a wide range of applications, including packaging for food, beverages, electronics, and consumer goods.In addition to being environmentally friendly, Pla molded parts offer several benefits over conventional plastics. They are heat-resistant, making them suitable for hot-fill applications, and they have excellent barrier properties, which help to preserve the freshness and quality of packaged products. Furthermore, the biodegradable nature of Pla molded parts ensures that they do not contribute to the accumulation of plastic waste in landfills and oceans.The launch of the new line of Pla molded parts represents a significant milestone for Pla Molded Parts Company in its commitment to sustainable packaging solutions. The company has invested heavily in research and development to create a range of products that meet the growing demand for environmentally friendly packaging options. By offering a viable alternative to traditional plastics, Pla Molded Parts Company is helping its customers reduce their environmental footprint and meet their sustainability goals."We are excited to introduce our new line of Pla molded parts, which represents a major advancement in sustainable packaging technology," said the CEO of Pla Molded Parts Company. "Our team has worked tirelessly to develop a product that not only meets the performance requirements of our customers but also aligns with our mission of environmental responsibility. We believe that the market is ripe for eco-friendly packaging solutions, and our Pla molded parts offer a compelling option for businesses looking to make a positive impact on the planet."The launch of the new line of Pla molded parts also underscores Pla Molded Parts Company's ongoing commitment to innovation and quality. The company has a state-of-the-art manufacturing facility equipped with the latest technology and production processes, enabling it to deliver high-quality products that meet the needs of its customers. Furthermore, Pla Molded Parts Company has a team of experienced engineers and designers who work closely with clients to develop customized solutions that address specific packaging challenges."We take great pride in our ability to deliver innovative and sustainable packaging solutions to our customers," said the CEO. "Our new line of Pla molded parts is a testament to our dedication to pushing the boundaries of what is possible in the packaging industry. We are confident that this product will not only meet the needs of our clients but also make a positive impact on the environment."As the demand for environmentally friendly packaging continues to grow, Pla Molded Parts Company is well-positioned to capitalize on this trend with its new line of Pla molded parts. The company's unwavering commitment to sustainability and innovation has cemented its reputation as a leader in the industry, and its latest product launch is further evidence of its dedication to providing cutting-edge solutions to its customers.In conclusion, the launch of the new line of Pla molded parts by Pla Molded Parts Company represents a significant step forward in the quest for sustainable packaging solutions. With its eco-friendly and high-performance properties, these molded parts offer a compelling alternative to traditional plastics, and they are poised to make a positive impact on the environment. As businesses and consumers increasingly prioritize sustainability, Pla Molded Parts Company's latest offering is well-positioned to meet the growing demand for environmentally friendly packaging solutions.
Top Tips for Plastic Injection Moulding
Plastic Injection Mould Technology Revolutionizes Manufacturing: A Look into the Innovative Solutions by [Company Name]In today's fast-paced world, manufacturing industries are constantly evolving and adapting to meet the demands of consumers. One company at the forefront of this revolution is [Company Name]. With their cutting-edge plastic injection mould technology, they have been able to provide innovative solutions for various industries.[Company Name] has been in the business for over two decades, and their expertise in plastic injection mould technology has made them a formidable force in the manufacturing industry. The company has consistently delivered high-quality products, and their commitment to innovation has allowed them to stay ahead of the competition.The plastic injection mould technology used by [Company Name] allows for the production of complex and intricate parts with high precision and efficiency. This technology has enabled the company to cater to a wide range of industries, from automotive to consumer electronics and medical devices.One of the key advantages of plastic injection mould technology is its versatility. It can be used to create a wide variety of products ranging from small, intricate parts to large components. This flexibility has allowed [Company Name] to serve a diverse clientele and meet the unique needs of each industry.Furthermore, the company's dedication to sustainability is evident in their manufacturing processes. By utilizing plastic injection mould technology, they are able to minimize material waste and energy consumption, thus reducing their environmental impact. This commitment to sustainability has not only benefited the environment but has also allowed the company to offer cost-effective solutions to their clients.In addition to their advanced technology, [Company Name] also prides itself on its team of highly skilled and experienced professionals. The company's engineers and technicians are well-versed in the latest developments in plastic injection mould technology, and they are able to deliver innovative solutions to even the most challenging manufacturing projects.One of the most notable achievements of [Company Name] is their recent collaboration with a leading automotive manufacturer. The company was able to design and manufacture a complex plastic component for the automotive industry using their state-of-the-art plastic injection mould technology. This collaboration not only showcased the company's technical expertise but also solidified their position as a trusted partner for the automotive industry.Looking ahead, [Company Name] is committed to staying at the forefront of plastic injection mould technology. The company is constantly investing in research and development to further enhance their manufacturing capabilities and provide even more innovative solutions for their clients.In conclusion, [Company Name] has proven to be a trailblazer in the manufacturing industry with their advanced plastic injection mould technology. Their dedication to innovation, sustainability, and quality has set them apart as a leader in the field. With their continued commitment to excellence, [Company Name] is poised to revolutionize the manufacturing industry for years to come.
CNC Machining Services for Aircraft Parts: Precision Manufacturing for Aviation Industry
Title: Revolutionizing Aircraft Manufacturing: Cutting-Edge CNC Machining Technology Takes FlightIntroduction:In the competitive aerospace industry, precision and reliability are paramount when it comes to aircraft manufacturing. Innovations in CNC machining have played a significant role in transforming the way aircraft parts are produced and assembled, leading to enhanced performance, reduced costs, and increased efficiency. This article explores the recent advancements in CNC machining technology and highlights the contributions of a pioneering company that has revolutionized the aerospace industry.Overview of CNC Machining in Aircraft Production:CNC machining, or Computer Numerical Control machining, is a specialized manufacturing process that utilizes computer software to control the movement of factory machinery and tools. This technology has dramatically improved the production of complex aircraft parts, enabling manufacturers to meet stringent quality and safety standards. The precision achieved by CNC machining makes it possible to fabricate intricate flight components with an unprecedented level of accuracy and consistency, reinforcing the overall structural integrity of modern aircraft.Breaking New Ground: A Leading CNC Machining Innovator:One company that stands apart in the field of CNC machining for aircraft parts is {}. With decades of experience and a passion for pushing technological boundaries, they have earned a remarkable reputation for their exceptional CNC machining capabilities. Over the years, the company has played a pivotal role in transforming aircraft manufacturing through groundbreaking processes, materials, and machining techniques.Cutting-Edge Technology Enhancing Aircraft Performance:By harnessing the power of CNC machining, {} has contributed to a myriad of advancements in aircraft manufacturing. For instance, their state-of-the-art machinery and innovative software enable them to create components with reduced weight, leading to improved fuel efficiency and enhanced performance. Through the precise machining of complex geometries, {} ensures that every part meets exact specifications, delivering optimal aerodynamic characteristics and reducing drag.Additionally, {} has invested heavily in research and development to devise advanced materials specifically designed for use in aerospace applications. This commitment has resulted in the production of lightweight but high-strength alloys that are crucial for ensuring structural integrity without compromising safety.Streamlining Manufacturing Processes for Efficiency:The implementation of CNC machining technology has streamlined the production process, significantly reducing the time required for manufacturing aircraft parts. The automation capabilities of CNC machines enable {} to handle large production volumes without sacrificing precision or quality. Furthermore, the utilization of advanced software allows for seamless integration between design and manufacturing systems, facilitating efficient collaboration and rapid prototyping.Ensuring Safety and Regulatory Compliance:Safety is of utmost importance in the aerospace industry, and {} has taken extensive measures to ensure the highest standards of compliance. The company adheres to rigorous quality control procedures during every stage of the manufacturing process. Through precise calibration and regular inspection of their CNC machines, {} guarantees that every part manufactured meets or exceeds industry regulations, providing peace of mind to both manufacturers and end-users.Global Impact of CNC Machining in Aircraft Manufacturing:The impact of CNC machining in the aerospace sector extends beyond a single company or region. By delivering consistent accuracy, rapid production rates, and superb quality, this technology has revolutionized the entire industry. With {} at the forefront of these advancements, manufacturers worldwide can now produce aircraft parts with increased efficiency, reduced costs, and uncompromising safety.Looking Towards the Future:As the aerospace industry continues to evolve and demand for aircraft parts increases, the role of CNC machining will only become more critical. The expertise and innovation demonstrated by {} have positioned them as a key player in the field. With ongoing research and development efforts, they are continually pushing the boundaries of CNC machining technology, opening up new possibilities for future aircraft manufacturing and setting new standards for precision, performance, and reliability.Conclusion:CNC machining has undoubtedly transformed the aircraft manufacturing process, elevating the industry to new heights of precision, efficiency, and safety. {} has played a pivotal role in this transformation, with their exceptional CNC machining technology leading to advancements in performance, reduced production time, and regulatory compliance. As they continue to push the limits of what is possible, the aerospace industry can confidently look forward to a future of even more groundbreaking achievements in CNC machining for aircraft manufacturing.
High-Quality Cnc Milled Aluminum Construction Level Frame
CNC Milled Aluminum Level Construction Level FrameThe construction industry is always evolving, and new technology is constantly being introduced to help improve the quality and efficiency of construction projects. One such advancement is the CNC milled aluminum level construction level frame, which is a game-changer in the industry.The CNC milled aluminum level construction level frame is a powerful tool that has been designed to ensure precision and accuracy in construction projects. It is made from high-quality aluminum and is machined using advanced CNC milling technology to create a strong and durable level frame that is capable of withstanding the rigors of the construction site.This level frame is designed to provide builders and contractors with a reliable and accurate tool that can be used to ensure that their construction projects are completed to the highest standards. The CNC milled aluminum construction level frame is lightweight and easy to handle, making it ideal for use in a wide range of construction applications.The precision machining of the aluminum frame ensures that it is perfectly flat and true, providing builders and contractors with a level surface to work with. This is essential for ensuring that building materials are installed correctly and that the finished construction is of the highest quality.In addition to its precision and accuracy, the CNC milled aluminum level construction level frame is also designed to be highly durable and long-lasting. The high-quality aluminum is resistant to corrosion and wear, ensuring that it will stand up to the demands of the construction site and provide reliable service for many years to come.The CNC milled aluminum level construction level frame is also designed to be easy to use, with simple and intuitive controls that allow builders and contractors to quickly and easily set the level to the desired position. This makes it easy to ensure that construction projects are completed with the highest level of accuracy and precision.{Company} is proud to introduce this innovative new product to the construction industry. With over {number} years of experience in the industry, {Company} has a strong reputation for providing high-quality construction tools and equipment. The CNC milled aluminum level construction level frame is the latest addition to their range of products, and it represents the company's commitment to innovation and excellence in the construction industry.{Company} has dedicated a significant amount of time and resources to developing the CNC milled aluminum level construction level frame, and they are confident that it will be a valuable tool for construction professionals. The company's team of engineers and designers have worked tirelessly to ensure that the level frame meets the highest standards of quality and performance, and they are excited to bring this cutting-edge technology to the construction market.In conclusion, the CNC milled aluminum level construction level frame is set to revolutionize the way construction projects are completed. With its precision machining, durability, and ease of use, it is sure to become an essential tool for builders and contractors. {Company}'s introduction of this innovative product demonstrates their commitment to providing the construction industry with the latest and most advanced tools and equipment.
Discover High-Quality Silicone Parts for Various Applications
Title: Revolutionizing the Industry – Innovative Silicone Parts (brand name removed) Sets New StandardsIntroduction (about 80 words):Silicone Parts, a pioneer in the silicone manufacturing industry, has been making waves with its groundbreaking products that are proving to be game-changers. With years of experience and expertise, the company is committed to delivering silicone parts that are not only high-quality but also technologically advanced, providing value to various industries. Let's explore further how Silicone Parts is revolutionizing the industry with its innovative solutions. Body:1. History and Expertise (about 120 words):Silicone Parts, founded in [year], has grown to become a leading name in the silicone manufacturing sector. Its success can be attributed to its unwavering commitment to quality, unmatched expertise, and continuous investment in research and development. Over the years, Silicone Parts has built a reputation for excellence in delivering cost-effective, durable, and efficient silicone parts for a wide range of applications, serving numerous industries, including automotive, healthcare, electronics, and more.2. Cutting-Edge Technology (about 150 words):Silicone Parts distinguishes itself from its competitors by staying ahead of the curve with its innovative use of cutting-edge technology. The company deploys state-of-the-art machinery and equipment in its manufacturing processes to ensure precision, consistency, and exceptional quality. By integrating advanced automation and robotics, Silicone Parts optimizes production efficiency without compromising on product excellence.3. Customization and Tailored Solutions (about 150 words):Understanding the unique requirements of different industries, Silicone Parts emphasizes the importance of customization. The company collaborates closely with its clients to develop tailored solutions that meet their specific needs. From concept to design to production, Silicone Parts provides comprehensive support, ensuring that their silicone parts align perfectly with customer expectations. This commitment to customization enables industries to achieve optimal performance and efficiency while reducing overall costs.4. Quality Assurance and Certifications (about 130 words):Silicone Parts places great emphasis on quality control systems to guarantee the reliability and longevity of their products. The company follows stringent quality assurance practices throughout the entire production process to maintain consistency and meet international standards. With certifications such as ISO 9001 and ISO 13485, Silicone Parts consistently proves its commitment to delivering excellence.5. Environmental Responsibility (about 140 words):As a responsible player in the silicone industry, Silicone Parts is constantly striving to minimize its environmental impact. The company adheres to strict sustainability practices, focusing on reducing waste, recycling, and implementing energy-efficient processes. Silicone Parts is actively involved in research and development initiatives to explore eco-friendly alternatives and ensure their products are eco-conscious.Conclusion (about 70 words):Silicone Parts serves as a catalyst for innovation, setting new standards within the silicone manufacturing industry. With its immense expertise, cutting-edge technology, commitment to customization, unwavering quality assurance, and sustainability efforts, the company aims to continue propelling the industry forward. Silicone Parts emerges as a trusted partner for industries aiming to optimize performance, enhance efficiency, and contribute to a greener future.
The Importance of Rapid Prototyping and Rapid Tooling in the Manufacturing Industry
Rapid Prototyping And Rapid Tooling, also known as 3D printing, have revolutionized the manufacturing industry in recent years. This cutting-edge technology allows businesses to create prototypes and tools quickly and cost-effectively, leading to streamlined production processes and faster time-to-market for new products. With the increasing demand for rapid prototyping and rapid tooling solutions, companies are turning to innovative industry leaders like {} to meet their manufacturing needs.{} is a leading provider of rapid prototyping and rapid tooling solutions, offering a wide range of services to help businesses bring their ideas to life. With state-of-the-art equipment and a team of highly skilled engineers and designers, {} has the capabilities to turn concepts into fully functional prototypes in a matter of days. Their innovative approach to manufacturing has helped countless businesses save time and money while bringing their products to market faster than ever before.One of the key advantages of rapid prototyping and rapid tooling is the ability to quickly iterate and refine designs. Traditional manufacturing methods can be time-consuming and costly, making it difficult for businesses to make changes to their products once they are in the production phase. However, with rapid prototyping, businesses can easily make modifications to their designs and test them out in real-world scenarios, allowing for greater innovation and improved product quality.In addition to rapid prototyping, {} also specializes in rapid tooling, which involves creating molds and other production tools using 3D printing technology. This allows businesses to quickly and cost-effectively produce tools that are customized to their specific manufacturing needs, further streamlining the production process and reducing lead times. By leveraging the power of rapid tooling, businesses can bring new products to market faster and more efficiently than ever before.The team at {} understands the complexities of the manufacturing industry and works closely with their clients to ensure that their unique needs are met. They offer a range of materials and finishing options to accommodate various product requirements, and their expertise in rapid prototyping and rapid tooling allows them to tackle even the most challenging projects with ease.With the increasing demand for rapid prototyping and rapid tooling solutions, {} has positioned themselves as a go-to source for businesses looking to streamline their manufacturing processes and bring new products to market quickly. Their commitment to innovation and quality has earned them a reputation as an industry leader, and their dedication to customer satisfaction has resulted in numerous successful partnerships with businesses across a wide range of industries.As technology continues to advance, the demand for rapid prototyping and rapid tooling solutions will only continue to grow. Businesses are constantly looking for ways to improve their production processes and bring new products to market faster, and companies like {} are at the forefront of this exciting industry. With their expertise and state-of-the-art facilities, {} is well-equipped to meet the evolving needs of businesses in an increasingly complex and competitive global marketplace.
Effective Ways to Cut Styrofoam for Your DIY Projects
Innovative Styrofoam Cutting Technology Revolutionizes Packaging IndustryIn today's rapidly evolving world, the need for sustainable and efficient packaging solutions has never been more critical. Thankfully, companies like {} are stepping up to the plate with innovative technologies that are revolutionizing the packaging industry. One such technology that is making waves is their state-of-the-art Styrofoam cutting technology, which is not only environmentally friendly but also provides superior performance compared to traditional packaging materials.The traditional method of cutting Styrofoam involves using hot wires or knives, which can be slow, imprecise, and generate a significant amount of waste. However, {} has developed a cutting-edge solution that addresses these issues and sets a new standard for Styrofoam processing. Their cutting technology utilizes advanced machinery and software to precisely cut and shape Styrofoam with speed and efficiency, while minimizing waste and energy consumption.One of the key advantages of {}'s Styrofoam cutting technology is its versatility. The machinery can be programmed to cut Styrofoam into a wide range of shapes and sizes, making it ideal for custom packaging applications. This level of flexibility allows companies to create packaging solutions that perfectly fit their products, reducing the need for excess materials and minimizing the overall environmental impact.In addition to its versatility, {}'s cutting technology also boasts impressive precision and speed. With the ability to cut complex designs with pinpoint accuracy, companies can achieve a level of consistency and quality that is simply unattainable with traditional cutting methods. Furthermore, the efficiency of the machinery ensures that production times are significantly reduced, allowing businesses to meet tight deadlines without compromising on quality.Perhaps the most significant benefit of {}'s Styrofoam cutting technology is its environmental impact. Traditional Styrofoam cutting methods are notorious for generating a substantial amount of waste, as well as consuming large amounts of energy. In contrast, {}'s cutting technology is designed to minimize waste and energy consumption, making it a much more sustainable option for companies looking to reduce their environmental footprint. By utilizing this cutting-edge technology, businesses can align themselves with the growing demand for eco-friendly packaging solutions and demonstrate their commitment to environmental stewardship.{}'s commitment to sustainability doesn't stop at their cutting technology. The company as a whole is dedicated to reducing its environmental impact and continuously seeks out innovative solutions to achieve this goal. From sourcing eco-friendly materials to implementing energy-efficient practices in their manufacturing processes, {} is leading the charge toward a more sustainable future for the packaging industry.Furthermore, {}'s dedication to innovation extends beyond their cutting technology. They are continually investing in research and development to explore new ways to enhance their products and processes, ensuring that they remain at the forefront of technological advancements in the industry. By staying ahead of the curve, {} is able to provide its customers with cutting-edge solutions that not only meet but exceed their needs and expectations.In conclusion, {}'s Styrofoam cutting technology represents a significant milestone in the packaging industry. By offering a versatile, precise, and sustainable solution for cutting Styrofoam, the company is empowering businesses to elevate their packaging capabilities and reduce their environmental impact. With a steadfast commitment to innovation and sustainability, {} is poised to lead the way in shaping a greener and more efficient future for the packaging industry.
High-Quality Complex Machining Parts for CNC Applications
CNC Complex Machining PartsIn today's world, precision engineering and manufacturing have become an integral part of many industries. From aerospace to automotive, medical to electronics, the demand for complex machining parts that meet stringent specifications is constantly on the rise. This is where CNC complex machining parts play a vital role in ensuring the success and efficiency of various manufacturing processes.ABC Company is a leading player in the field of CNC complex machining parts, with a stellar reputation for delivering high-quality, precision-engineered components to a wide range of industries. The company has been at the forefront of innovation and technology in the field of precision engineering, constantly pushing the boundaries of what can be achieved with CNC machining.ABC Company's state-of-the-art facility is equipped with the latest CNC machining technology, including advanced multi-axis milling machines, turning centers, and EDM machines. This allows the company to produce complex parts with unparalleled accuracy and consistency, meeting the most stringent tolerances and specifications.One of the key strengths of ABC Company is its ability to work with a wide range of materials, including exotic alloys, stainless steel, aluminum, and plastic. This versatility enables the company to serve a diverse customer base and cater to a wide variety of industry requirements. Whether it's a complex aerospace component or a medical device part, ABC Company has the expertise and capability to deliver precision-engineered solutions.The company's team of highly skilled engineers and machinists are well-versed in the latest CAD/CAM software and are adept at creating intricate, complex geometries that push the boundaries of what is possible with CNC machining. This expertise, combined with the company's commitment to quality and customer satisfaction, has earned ABC Company a reputation for being a trusted partner in the precision engineering industry.ABC Company's dedication to quality and precision is further evident in its rigorous quality control processes. Every component produced undergoes thorough inspection and testing to ensure that it meets the highest standards of accuracy and quality. This commitment to quality has earned the company numerous certifications and accolades, making it a preferred choice for customers who demand the best in CNC complex machining parts.In addition to its manufacturing capabilities, ABC Company also offers comprehensive design and engineering services to its customers. The company's team of experienced engineers collaborate closely with customers to understand their specific requirements and to provide customized solutions that meet their unique needs. This customer-centric approach has helped ABC Company build long-lasting relationships with its clients and has positioned the company as a trusted partner in their success.Looking towards the future, ABC Company is committed to staying at the forefront of CNC complex machining technology and innovation. The company continues to invest in the latest CNC machining equipment and software, as well as in the training and development of its personnel, to ensure that it remains a leader in the precision engineering industry.With its unwavering commitment to quality, precision, and customer satisfaction, ABC Company is well-positioned to meet the evolving demands of the manufacturing industry and to continue delivering cutting-edge CNC complex machining parts to its valued customers.